Key Takeaways
1. Quality Improvement: A Paradigm Shift in Management
Quality can be defined only in terms of the agent. Who is the judge of quality?
A new economic age. The traditional Western management style, focused on short-term profits and quick fixes, is no longer sufficient in today's competitive global market. Deming proposes a radical transformation in management thinking, emphasizing long-term sustainability and continuous improvement.
The quality chain reaction. Improving quality leads to decreased costs, increased productivity, and greater market share. This chain reaction results in job creation and better return on investment. By focusing on quality, companies can break free from the vicious cycle of declining competitiveness and job losses.
Customer focus. Quality must be defined from the customer's perspective. This requires:
- Understanding customer needs and expectations
- Designing products and services to meet these needs
- Continuously improving based on customer feedback
- Recognizing that the customer is the most important part of the production line
2. The 14 Points for Transformation of Western Management
Adoption and action on the 14 points are a signal that the management intend to stay in business and aim to protect investors and jobs.
Fundamental change. Deming's 14 points provide a comprehensive framework for transforming management practices. These points are not a checklist but a interconnected system of principles that must be adopted holistically.
Key principles include:
- Creating constancy of purpose for improvement
- Adopting the new philosophy of quality
- Ceasing dependence on mass inspection
- Ending the practice of awarding business solely on price
- Constantly improving the system of production and service
- Instituting leadership and training
- Driving out fear in the workplace
- Breaking down barriers between departments
- Eliminating slogans, exhortations, and numerical quotas
- Removing barriers to pride of workmanship
- Instituting a vigorous program of education and self-improvement
3. Common Causes vs. Special Causes: Understanding Variation
Costly confusion. Confusion between common causes and special causes leads to frustration of everyone, and leads to greater variability and to higher costs, exactly contrary to what is needed.
Types of variation. Deming distinguishes between two types of variation in processes:
- Common causes: Inherent in the system, affecting all workers and products
- Special causes: Specific, identifiable factors that are not part of the regular system
Management responsibility. The vast majority (94%) of problems in an organization stem from common causes, which are the responsibility of management to address. Only 6% are due to special causes, which can often be addressed by workers themselves.
Avoiding tampering. Misunderstanding the nature of variation leads to "tampering" - making adjustments to a stable process based on normal fluctuations. This often results in increased variability and decreased quality. Proper statistical analysis is crucial for distinguishing between common and special causes, allowing for appropriate action.
4. The Deadly Diseases and Obstacles to Transformation
Transformation of American style of management is not a job of reconstruction, nor is it revision. It requires a whole new structure, from foundation upward.
Major impediments. Deming identifies several "deadly diseases" that plague Western management:
- Lack of constancy of purpose
- Emphasis on short-term profits
- Evaluation of performance, merit rating, or annual review
- Mobility of management
- Running a company on visible figures alone
Additional obstacles include:
- The search for examples (believing success can be copied without understanding)
- The supposition that solving problems, automation, and new machinery will transform industry
- Obsolete schools and incorrect teaching of statistical methods
- Reliance on quality control departments to "fix" all quality issues
- The belief that "our problems are different"
Overcoming barriers. Recognizing and addressing these diseases and obstacles is crucial for successful transformation. It requires a fundamental shift in thinking and a long-term commitment to change.
5. Statistical Process Control: The Key to Quality and Productivity
A statistical chart detects the existence of a cause of variation that lies outside the system. It does not find the cause.
Understanding process capability. Statistical Process Control (SPC) provides a method for understanding and improving processes. By using control charts, managers can:
- Distinguish between common and special causes of variation
- Identify when a process is in statistical control (stable and predictable)
- Determine the capability of a process to meet specifications
Benefits of stability. A process in statistical control:
- Has a definable identity and predictable performance
- Allows for accurate cost prediction
- Enables focused improvement efforts
- Simplifies relationships with suppliers
- Facilitates the implementation of just-in-time production systems
Continuous improvement. Once a process is in control, efforts can be directed towards improving its capability through systematic experimentation and analysis.
6. The Importance of Operational Definitions in Quality Management
An operational definition puts communicable meaning into a concept.
Clear communication. Operational definitions are essential for effective quality management. They provide:
- A specific test or measurement procedure
- Criteria for judgment
- A clear decision-making process
Avoiding misunderstandings. Without operational definitions, terms like "quality," "reliable," or "safe" become subjective and open to interpretation. This leads to miscommunication between:
- Suppliers and customers
- Different departments within an organization
- Management and workers
Examples of operational definitions:
- Defining "on-time delivery" as "arrival within 15 minutes of scheduled time"
- Specifying "acceptable quality" as "no more than 3 defects per 1000 units"
- Measuring "customer satisfaction" through a specific survey process with defined scoring criteria
7. Transforming Service Organizations Through Quality Principles
The principles explained here, along with the chain reaction displayed on page 3, the flow diagram in Fig. 1, and techniques taught to hundreds of engineers, commenced the transformation of Japanese industry.
Applicability to services. Deming's principles are not limited to manufacturing but are equally relevant to service industries. This includes:
- Healthcare
- Education
- Government services
- Retail and hospitality
- Financial services
Key considerations for services:
- Defining and measuring quality in intangible outputs
- Managing customer interactions and perceptions
- Adapting statistical methods to service processes
- Focusing on system-wide improvement rather than individual performance
Examples of application:
- Reducing patient waiting times in hospitals
- Improving accuracy and speed in financial transactions
- Enhancing customer satisfaction in hospitality services
- Streamlining government processes to reduce bureaucracy
8. The Fallacy of Management by Objectives and Numerical Goals
Eliminate work standards (quotas) on the factory floor. Substitute leadership.
Harmful effects. Management by objectives (MBO) and numerical quotas often lead to:
- Short-term thinking and suboptimization
- Manipulation of figures to meet targets
- Decreased quality and employee morale
- Inhibition of continuous improvement
Focus on the process. Instead of setting arbitrary numerical goals, management should:
- Understand and improve the underlying processes
- Provide leadership and resources for improvement
- Foster an environment of learning and innovation
- Recognize that most variation comes from the system, not individual workers
Alternative approaches:
- Use statistical methods to understand process capability
- Set goals for improvement of the system, not numerical targets
- Encourage experimentation and learning
- Recognize and reward efforts to improve the process, not just results
9. Continuous Improvement: The Never-Ending Cycle of Quality
Improvement of quality transfers waste of man-hours and of machine-time into the manufacture of good product and better service.
The Shewhart Cycle. Deming popularized the Plan-Do-Study-Act (PDSA) cycle, also known as the Deming Cycle, as a framework for continuous improvement:
- Plan: Identify opportunities and plan changes
- Do: Implement changes on a small scale
- Study: Analyze the results and learn from the change
- Act: Adopt, adapt, or abandon the change based on results
Never-ending improvement. Quality improvement is not a one-time event but a continuous process. This requires:
- A long-term perspective and commitment
- Willingness to challenge existing methods and assumptions
- Systematic approach to problem-solving and innovation
- Involvement of all employees in the improvement process
Examples of continuous improvement:
- Regular review and updating of processes
- Ongoing training and education programs
- Systematic gathering and analysis of customer feedback
- Benchmarking against industry best practices
10. Leadership and Training: Cornerstones of Quality Management
The aim of leadership should be to improve the performance of man and machine, to improve quality, to increase output, and simultaneously to bring pride of workmanship to people.
Transformational leadership. Quality improvement requires a new style of leadership that:
- Focuses on long-term vision and system improvement
- Empowers employees to take pride in their work
- Removes barriers to effective performance
- Fosters a culture of continuous learning and improvement
Importance of training. Effective quality management requires ongoing education and training at all levels of the organization:
- Management must learn statistical thinking and quality principles
- Workers need training in problem-solving and process improvement techniques
- Cross-functional training helps break down departmental barriers
- Continuous learning is essential to adapt to changing market conditions
Key leadership actions:
- Clearly communicate the organization's vision and quality philosophy
- Provide resources and support for improvement efforts
- Lead by example in embracing new methods and thinking
- Recognize and celebrate improvements and learning, not just results
- Create an environment where it's safe to experiment and learn from mistakes
Last updated:
FAQ
What's Out of the Crisis about?
- Management Transformation: The book emphasizes the need for a complete overhaul of American management practices to enhance quality and productivity, crucial for survival in a global market.
- 14 Points for Management: Deming introduces 14 principles that serve as a framework for fostering a culture of quality and continuous improvement within organizations.
- Systemic Issues: It addresses systemic problems like short-term profit focus and lack of constancy of purpose, which lead to inefficiencies and economic harm.
Why should I read Out of the Crisis?
- Learn from a Pioneer: W. Edwards Deming is a key figure in quality management, and his insights have significantly influenced industries worldwide.
- Practical Framework: The book offers actionable steps for managers to improve their organizations through the 14 points and discussions on diseases and obstacles.
- Quality and Productivity: It provides a deep understanding of the relationship between quality and productivity, essential for anyone involved in management or operations.
What are the key takeaways of Out of the Crisis?
- Quality as a Process: Quality is a continuous process that must be integrated into every aspect of an organization, beginning with management's intent.
- Management's Role: Improvement of quality is primarily the responsibility of management, which must create a stable system that fosters quality.
- Long-term Commitment: Organizations must commit to long-term learning and improvement, as quick results are unrealistic and lead to disappointment.
What are the 14 points for management in Out of the Crisis?
- Constancy of Purpose: Develop a long-term vision focused on improving products and services to remain competitive, prioritizing quality over short-term profits.
- Adopt the New Philosophy: Embrace a new economic age that prioritizes quality and productivity, requiring a mindset shift for both management and employees.
- Cease Dependence on Inspection: Build quality into the product from the start, rather than relying on inspection to catch defects, advocating for proactive quality management.
What are the diseases and obstacles discussed in Out of the Crisis?
- Deadly Diseases: Deming identifies issues like lack of constancy of purpose and short-term profit focus, which undermine quality and productivity.
- Obstacles to Improvement: Factors such as management's reliance on visible figures and the mobility of management contribute to instability and lack of focus.
- Systemic Change Needed: Addressing these diseases and obstacles requires a fundamental change in management practices and organizational culture.
How does Deming define quality in Out of the Crisis?
- Quality as a Systematic Process: Quality is a continuous process integrated into every stage of production and service, focusing on fulfilling customer needs.
- Customer Focus: The ultimate measure of quality is customer satisfaction, emphasizing the need to understand and meet customer expectations.
- Reduction of Variation: Quality improvement involves reducing variation in processes and outputs, managing sources of variation effectively.
What is the significance of the Shewhart cycle in Out of the Crisis?
- Foundation for Improvement: The Shewhart cycle (Plan-Do-Study-Act) is a framework for continuous improvement, encouraging systematic testing and learning.
- Data-Driven Decisions: It emphasizes using data to inform decisions and improve processes, with a focus on understanding variation.
- Broad Application: The cycle is applicable across industries, including manufacturing, services, and government, benefiting all organizations.
How does Out of the Crisis address the relationship between quality and productivity?
- Interconnectedness: Improving quality leads to increased productivity, as better quality results in lower costs and improved competitive position.
- Chain Reaction: The book describes a chain reaction where quality improvement leads to more jobs and economic benefits.
- System Improvement Focus: Management must focus on improving the system to enhance both quality and productivity.
What is Deming's philosophy on management and quality?
- Management's Responsibility: Management must actively foster a culture of quality, as their failure to do so is the prime cause of trouble.
- Continuous Improvement: Organizations should adopt a continuous improvement mindset, encapsulated in the Plan-Do-Study-Act cycle.
- Employee Involvement: All employees should be involved in quality initiatives, equipped with the tools and training to take pride in their work.
How does Deming define statistical process control?
- Monitoring Variation: Statistical process control (SPC) uses statistical methods to monitor and control a process, with control charts as a key tool.
- Identifying Causes: SPC helps identify special causes of variation, allowing for appropriate corrective actions.
- Predictable Outcomes: A process in statistical control produces predictable outcomes, aiding in better planning and resource allocation.
How can organizations implement the principles from Out of the Crisis?
- Leadership Commitment: Top management must commit to adopting the 14 points and addressing deadly diseases, actively participating in the transformation.
- Education and Training: Invest in education and training for all employees to understand quality management principles and statistical methods.
- Culture of Improvement: Foster an environment where employees feel empowered to contribute to quality improvement efforts, emphasizing collective responsibility.
What is the significance of the "red bead experiment" in Out of the Crisis?
- Systemic Issues: The experiment illustrates how systemic issues lead to poor quality outcomes, showing that workers are often not to blame.
- Understanding Variation: It helps participants understand variation and its impact on performance, demonstrating that variation is natural.
- Management's Role: Emphasizes the need for management to create systems that minimize variation and improve quality, addressing systemic problems.
Review Summary
Out of the Crisis is highly regarded as a seminal work on quality management and leadership. Readers praise Deming's insights into improving organizational systems, statistical analysis, and long-term thinking. Many find the ideas still relevant today, though some note the writing can be dry or repetitive. The book is seen as essential reading for managers and leaders, offering timeless principles for creating constancy of purpose, driving out fear, and fostering continuous improvement. While focused on manufacturing, readers find applications across industries.
Similar Books
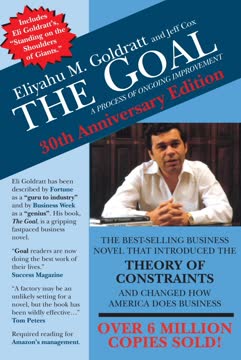
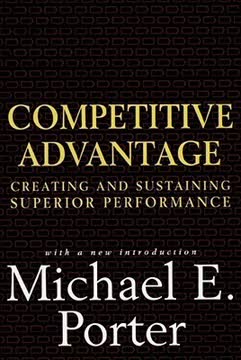
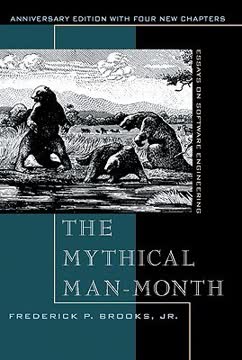
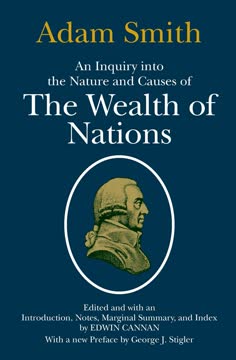
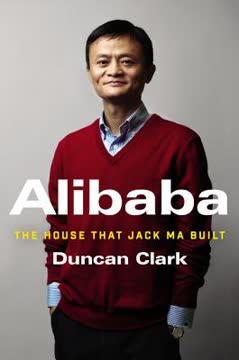
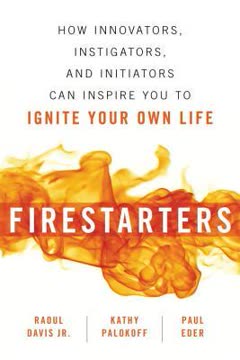
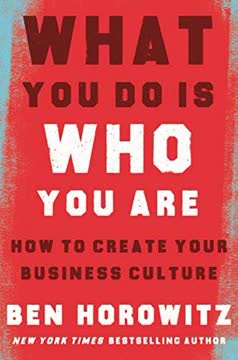
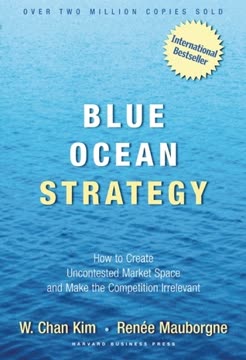
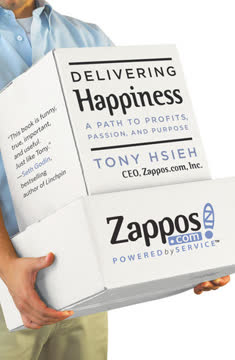
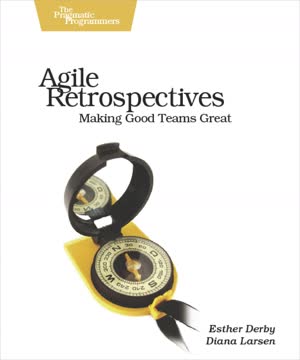
Download PDF
Download EPUB
.epub
digital book format is ideal for reading ebooks on phones, tablets, and e-readers.