Key Takeaways
1. Flow, Synchronization, and Leveling (FSL) are the pillars of lean strategy
"FSL encompasses the must-have criteria proposed to assess and audit the lean status of a company."
Flow is the cornerstone of lean operations. It refers to the smooth, uninterrupted movement of materials, information, and processes from start to finish. Synchronization ensures that each step in the process is aligned with customer demand, while leveling distributes work evenly to prevent overburden and unevenness.
Key aspects of FSL:
- Flow: Eliminates waste, reduces lead time, and improves quality
- Synchronization: Aligns production with customer demand
- Leveling: Distributes workload evenly, reducing stress on people and equipment
Implementing FSL requires a holistic approach, involving every aspect of the organization from production to supply chain management. Companies that successfully adopt FSL can achieve significant improvements in efficiency, quality, and customer satisfaction.
2. Traditional companies are cursed by their own system of overproduction
"Traditional companies employ maximum resources for minimum outputs, while lean companies employ minimum resources for maximum outputs."
Overproduction is the root of all evil in manufacturing. Traditional companies often produce based on forecasts, leading to excess inventory, long lead times, and increased costs. This approach is driven by the misguided belief that producing in large batches is more efficient.
Consequences of traditional production methods:
- High inventory levels
- Increased storage costs
- Quality issues due to long storage times
- Reduced flexibility to respond to market changes
- Wasted resources on non-value-adding activities
Lean companies, in contrast, produce only what is needed, when it is needed, and in the amount needed. This approach minimizes waste, improves quality, and increases flexibility to meet customer demands.
3. Lean strategy prioritizes customer satisfaction over shareholder value
"The ultimate objective of a company is solely to realize customer satisfaction, which assures the ongoing sustainability of the company."
Customer-first approach is at the heart of lean strategy. While traditional companies often prioritize short-term shareholder value, lean companies focus on delivering value to customers, believing that this approach leads to long-term success and sustainability.
Benefits of prioritizing customer satisfaction:
- Improved product quality and service
- Increased customer loyalty
- Better alignment of company resources with customer needs
- Long-term financial stability and growth
- Enhanced reputation and brand value
By focusing on customer satisfaction, lean companies create a virtuous cycle that ultimately benefits all stakeholders, including shareholders, employees, and the community.
4. The CEO and board are crucial for embracing and sustaining lean strategy
"If the lean introduction is started and terminated after three months, nothing would remain after three days of operations no matter how many improvements were made during the first three months."
Top-level commitment is essential for successful lean transformation. The CEO and board must not only initiate the lean journey but also provide ongoing support and resources to sustain it. Without this commitment, lean initiatives often fail or produce only short-term results.
Key responsibilities of leadership in lean transformation:
- Setting a clear vision and strategy for lean implementation
- Allocating necessary resources for training and improvement activities
- Regularly reviewing progress and addressing obstacles
- Leading by example and participating in improvement activities
- Fostering a culture of continuous improvement throughout the organization
Leadership must view lean as a long-term strategy rather than a quick fix, understanding that true transformation takes years of consistent effort and commitment.
5. Gemba (the real place) is where value is created and problems are solved
"Go to the gemba when problems arise."
Gemba-focused management emphasizes the importance of understanding what's happening on the shop floor or wherever work is being done. Leaders and managers should regularly visit the gemba to observe processes, identify problems, and work with employees to find solutions.
Benefits of gemba-focused management:
- Direct observation of processes and problems
- Improved communication between management and workers
- Faster problem-solving and decision-making
- Enhanced employee engagement and empowerment
- Better understanding of customer needs and value creation
By going to the gemba, leaders can make informed decisions based on real data and observations rather than relying solely on reports or assumptions.
6. Kaizen (continuous improvement) is the foundation of lean operations
"Kaizen ideas are infinite. Don't think you have made things better than before and be at ease."
Continuous improvement is a never-ending process that involves everyone in the organization. Kaizen encourages employees at all levels to identify and implement small, incremental improvements in their daily work.
Key aspects of kaizen:
- Empowering employees to identify and solve problems
- Focusing on small, frequent improvements rather than big, infrequent changes
- Creating a culture of learning and experimentation
- Emphasizing process improvement over blame
- Recognizing and celebrating improvement efforts
Kaizen helps organizations adapt to changing market conditions, improve quality and efficiency, and maintain a competitive edge. It also fosters a positive work environment where employees feel valued and engaged.
7. Just-in-Time (JIT) production minimizes waste and maximizes efficiency
"JIT means to provide what is needed (material), when it is needed (timing), and as many as needed (volume)."
JIT production aligns production with customer demand, reducing inventory and waste. This approach requires careful coordination of all aspects of the production process, from suppliers to final assembly.
Key elements of JIT production:
- Pull system based on actual customer orders
- Small lot sizes and frequent deliveries
- Quick changeovers to enable production flexibility
- Close relationships with suppliers
- Balanced and synchronized production lines
JIT production helps companies reduce costs, improve quality, and respond quickly to changes in customer demand. However, it requires a high level of discipline and coordination throughout the supply chain.
8. Standardization and visual management enable continuous improvement
"Where there is no standard, there can be no kaizen."
Standardization provides a baseline for improvement, while visual management makes problems and progress visible to all. Together, these practices create a foundation for continuous improvement.
Benefits of standardization and visual management:
- Clear expectations for work processes
- Easier identification of deviations and problems
- Faster training of new employees
- Improved communication across shifts and departments
- Enhanced ability to measure and track improvements
By establishing clear standards and making information visible, organizations can more easily identify opportunities for improvement and track progress over time.
9. Jidoka (automation with a human touch) prevents defects and overproduction
"An 'automatic' machine is one that will stop the moment the operation is over or an abnormality has occurred."
Jidoka combines automation with human intelligence to detect and prevent defects. This concept ensures that quality is built into the process rather than inspected after production.
Key aspects of jidoka:
- Automatic detection of abnormalities
- Immediate stoppage when problems occur
- Clear signaling of problems (e.g., andon lights)
- Empowerment of operators to stop the line
- Root cause analysis and permanent countermeasures
Jidoka helps prevent defects from being passed down the production line, reduces the need for inspection, and enables operators to manage multiple machines efficiently.
10. Lean strategy requires a long-term commitment and cultural transformation
"Changing the traditional mindset into lean is a long-term project. The lean introduction involves both functional and operational improvements, which take many years and even decades."
Cultural transformation is essential for successful lean implementation. It requires a shift in mindset from short-term, results-oriented thinking to long-term, process-oriented improvement.
Key elements of lean cultural transformation:
- Long-term perspective on improvement and results
- Emphasis on developing people and their problem-solving skills
- Respect for front-line workers and their ideas
- Focus on process improvement rather than blame
- Leadership commitment to lean principles and practices
Organizations must understand that lean is not just a set of tools but a fundamental change in how they operate and think about value creation. This transformation requires patience, persistence, and a willingness to challenge deeply ingrained assumptions and practices.
Last updated:
Review Summary
Strategic Kaizen explores operational excellence using Flow Synchronization and Leveling assessment. Readers appreciate its focus on continuous improvement and Toyota's success story. The book emphasizes reducing waste, improving customer satisfaction, and making small, consistent improvements. Some found the content familiar or too manufacturing-focused. It discusses the importance of long-term value creation over short-term goals and suggests reporting operational performance alongside financial results. Overall, readers found it insightful, though some desired more diverse industry examples.
Similar Books
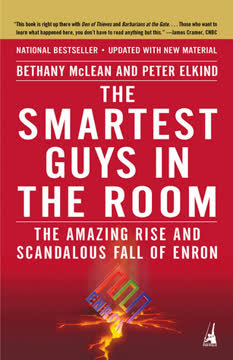
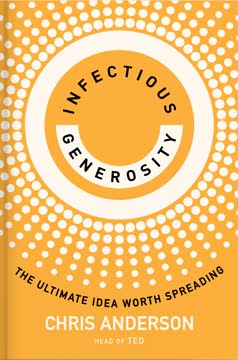
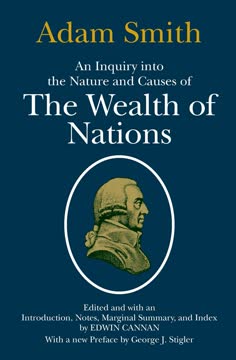
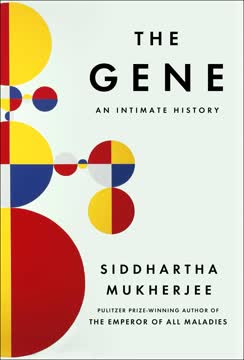
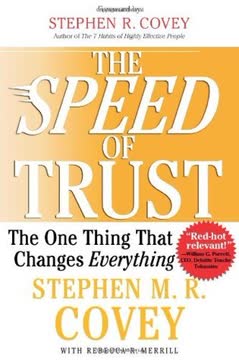
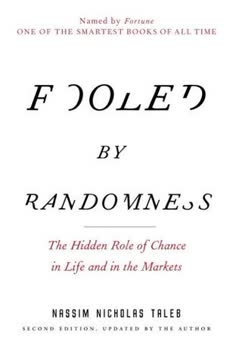
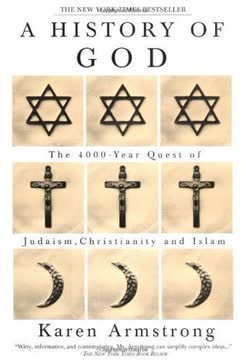
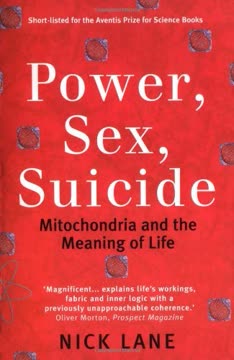
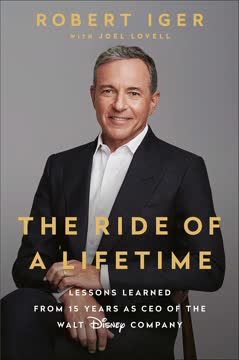
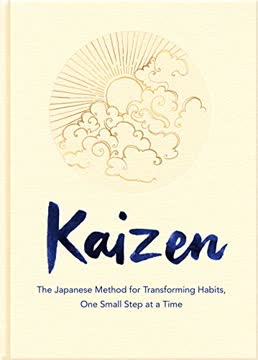
Download PDF
Download EPUB
.epub
digital book format is ideal for reading ebooks on phones, tablets, and e-readers.