Puntos clave
1. El Método Toyota: Una Filosofía de Excelencia a Largo Plazo
La obtención de un rendimiento empresarial por parte de la empresa matriz a través de la intimidación a los proveedores es totalmente ajena al espíritu del Sistema de Producción Toyota.
Pensamiento a largo plazo. El Método Toyota no se trata solo de herramientas y técnicas, sino de una filosofía integral centrada en la excelencia a largo plazo. Este enfoque prioriza la creación de valor para los clientes, la sociedad y la economía por encima de los objetivos financieros a corto plazo. El éxito de Toyota proviene de su compromiso con:
- Desarrollar personas
- Mejorar continuamente los procesos
- Resolver problemas de raíz
- Construir relaciones sólidas con socios y proveedores
El liderazgo de Toyota refuerza constantemente estos principios, asegurando que permeen cada aspecto de la organización. Esta perspectiva a largo plazo permite a Toyota resistir las recesiones económicas y salir más fuerte, como lo demuestra su capacidad para mantener la rentabilidad y la cuota de mercado incluso en tiempos difíciles.
2. Flujo Continuo: Eliminando Desperdicios y Revelando Problemas
Si tienes un proyecto que se supone debe implementarse completamente en un año, me parece que la típica empresa estadounidense gastará alrededor de tres meses en planificación, luego comenzarán a implementar. Pero se encontrarán con todo tipo de problemas después de la implementación, y gastarán el resto del año corrigiéndolos.
Eficiencia a través del flujo. El enfoque de Toyota hacia el flujo continuo se centra en eliminar desperdicios (muda) y crear un proceso de producción fluido. Este concepto se extiende más allá de la fabricación a todos los aspectos del negocio. Los elementos clave incluyen:
- Flujo de una pieza: Mover productos a través de los procesos uno a la vez
- Tiempo takt: Alinear el ritmo de producción con la demanda del cliente
- Fabricación celular: Organizar equipos y estaciones de trabajo en secuencia
Al implementar el flujo continuo, Toyota:
- Reduce inventarios y sobreproducción
- Mejora la calidad al identificar y abordar rápidamente los defectos
- Aumenta la productividad y reduce los tiempos de entrega
- Mejora la flexibilidad para responder a cambios en la demanda
Este enfoque obliga a que los problemas salgan a la superficie, permitiendo una resolución inmediata y una mejora continua.
3. Sistemas Pull: Producir Solo lo Necesario
Cuanto más inventario tiene una empresa, … menos probable es que tenga lo que necesita.
Producción justo a tiempo. El sistema pull de Toyota, también conocido como kanban, asegura que la producción esté impulsada por la demanda real del cliente en lugar de pronósticos. Este enfoque:
- Minimiza inventarios y costos asociados
- Mejora el flujo de caja al reducir el trabajo en proceso
- Aumenta la flexibilidad para responder a cambios en el mercado
- Simplifica la programación y reduce la sobreproducción
El sistema pull funciona utilizando señales visuales (tarjetas kanban) para activar la producción o el movimiento de materiales solo cuando son necesarios por el siguiente proceso. Esto crea una reacción en cadena a lo largo de la cadena de suministro, asegurando que cada paso produzca solo lo que se requiere en el siguiente.
- En fabricación: Las piezas se producen solo cuando son señaladas por procesos posteriores
- En servicios: El trabajo se inicia solo cuando es solicitado por el cliente o el siguiente paso
- En desarrollo de productos: Las etapas de diseño avanzan según el "pull" de fases posteriores
4. Nivelación de la Carga de Trabajo: La Clave para la Verdadera Eficiencia
Trabaja como la tortuga, no como la liebre.
Producción equilibrada. Heijunka, o nivelación de la producción, es un concepto crucial en el Sistema de Producción Toyota. Implica:
- Distribuir el volumen y la mezcla de producción de manera uniforme a lo largo del tiempo
- Reducir picos y valles en el cronograma de producción
- Minimizar la sobrecarga de personas y equipos (muri)
- Eliminar la irregularidad en el cronograma de producción (mura)
Al nivelar la carga de trabajo, Toyota logra:
- Calidad consistente al evitar producciones apresuradas
- Eficiencia mejorada y reducción de desperdicios
- Mejor utilización de recursos y equipos
- Mayor capacidad para satisfacer la demanda del cliente con tiempos de entrega más cortos
Este enfoque puede parecer contraintuitivo para quienes se centran en maximizar la eficiencia a corto plazo, pero conduce a una mayor productividad y estabilidad en el largo plazo.
5. Incorporando Calidad en los Procesos: Detenerse y Solucionar Problemas
Valoramos en gran medida la implementación real y la acción. Hay muchas cosas que uno no entiende y, por lo tanto, les preguntamos por qué no simplemente actúan; ¿por qué no intentan hacer algo?
Calidad en la fuente. El compromiso de Toyota de incorporar calidad en sus procesos se ejemplifica en el principio jidoka, que empodera a los trabajadores para detener la producción cuando detectan anormalidades. Este enfoque:
- Previene que los defectos avancen
- Fomenta la resolución inmediata de problemas
- Mejora la calidad general y reduce el retrabajo
Los elementos clave de este principio incluyen:
- Cuerdas Andon: Permiten a los trabajadores señalar problemas y detener la línea
- Poka-yoke: Dispositivos a prueba de errores que previenen equivocaciones
- Análisis de causa raíz: Resolución sistemática de problemas utilizando técnicas como los "5 Porqués"
Al centrarse en incorporar calidad en cada proceso, Toyota reduce costos generales y mejora la satisfacción del cliente, a pesar de la aparente ineficiencia de detener la producción para abordar problemas.
6. Tareas Estandarizadas: La Base para la Mejora Continua
Utiliza métodos estables y repetibles en todas partes para mantener la previsibilidad, el tiempo regular y la producción regular de tus procesos. Es la base para el flujo y el pull.
La consistencia genera mejora. El trabajo estandarizado es una piedra angular del Sistema de Producción Toyota, proporcionando una base para la mejora continua. Implica:
- Documentar la mejor práctica actual para cada proceso
- Asegurar un rendimiento consistente independientemente de quién realice la tarea
- Crear una base para el kaizen (mejora continua)
Los beneficios del trabajo estandarizado incluyen:
- Calidad mejorada y reducción de variabilidad
- Entrenamiento más fácil de nuevos empleados
- Expectativas claras para el rendimiento
- Un punto de partida para la resolución de problemas y la innovación
Toyota ve la estandarización no como un conjunto rígido de reglas, sino como una herramienta dinámica que evoluciona con cada mejora. Este enfoque permite tanto estabilidad como flexibilidad en las operaciones.
7. Control Visual: Haciendo Visibles los Problemas
Utiliza el control visual para que no haya problemas ocultos.
Claridad a través de la visualización. El control visual es un principio clave en el Método Toyota, haciendo que el estado de los procesos sea inmediatamente aparente para todos. Este enfoque:
- Facilita la identificación rápida de anormalidades
- Mejora la comunicación y la coordinación
- Apoya el trabajo estandarizado y la resolución de problemas
Ejemplos de control visual en Toyota incluyen:
- Tableros Andon: Muestran el estado de las líneas de producción
- Tarjetas kanban: Señalan la necesidad de piezas o materiales
- Organización del lugar de trabajo 5S: Asegura que todo tenga un lugar visible y designado
- Informes A3: Resumen información compleja en una sola página
Al hacer visibles los procesos y su estado, Toyota crea un entorno donde los problemas no pueden ocultarse, permitiendo una respuesta rápida y una mejora continua.
8. Tecnología que Sirve a las Personas y a los Procesos
Utiliza la tecnología para apoyar a las personas, no para reemplazarlas. A menudo, es mejor trabajar un proceso manualmente antes de agregar tecnología para respaldar el proceso.
Tecnología centrada en el ser humano. El enfoque de Toyota hacia la tecnología enfatiza el apoyo a los trabajadores humanos en lugar de reemplazarlos. Esta filosofía asegura que:
- La tecnología mejore y no obstaculice las capacidades humanas
- Los procesos se comprendan a fondo antes de la automatización
- Las inversiones en tecnología se evalúen cuidadosamente para el beneficio a largo plazo
El proceso de adopción de tecnología de Toyota incluye:
- Probar exhaustivamente nuevas tecnologías antes de su implementación
- Asegurar que la tecnología se alinee con los procesos y filosofías existentes
- Priorizar la fiabilidad y flexibilidad sobre características de vanguardia
Este enfoque ha permitido a Toyota mantener un equilibrio entre el avance tecnológico y la habilidad humana, resultando en un sistema de producción más robusto y adaptable.
9. Desarrollando Personas y Equipos Excepcionales
Valoramos en gran medida la implementación real y la acción. Hay muchas cosas que uno no entiende y, por lo tanto, les preguntamos por qué no simplemente actúan; ¿por qué no intentan hacer algo?
Organización centrada en las personas. El éxito de Toyota se basa en su capacidad para desarrollar individuos y equipos excepcionales que encarnan la filosofía de la empresa. Esto implica:
- Inversión a largo plazo en el desarrollo de empleados
- Promoción interna para mantener la continuidad cultural
- Equilibrar la excelencia individual con un trabajo en equipo efectivo
Los aspectos clave del desarrollo de personas en Toyota incluyen:
- Capacitación en el trabajo y mentoría
- Experiencia multifuncional y rotación de puestos
- Fomento de la resolución de problemas en todos los niveles
- Énfasis en el aprendizaje y la mejora continua
Al desarrollar personas que entienden y viven el Método Toyota, la empresa asegura que su filosofía y prácticas se mantengan y evolucionen con el tiempo.
10. Respetando y Desafiando a los Proveedores
Ten respeto por tus socios y proveedores y trátalos como una extensión de tu negocio.
Asociaciones colaborativas. El enfoque de Toyota hacia las relaciones con los proveedores se basa en el respeto mutuo y la asociación a largo plazo. Esto implica:
- Tratar a los proveedores como una extensión del propio negocio de Toyota
- Desafiar a los proveedores a mejorar y crecer
- Proporcionar apoyo y compartir conocimientos para ayudar a los proveedores a tener éxito
Las prácticas de desarrollo de proveedores de Toyota incluyen:
- Resolución conjunta de problemas y actividades de mejora continua
- Compartición de mejores prácticas y tecnología
- Compromisos a largo plazo que fomentan la inversión de los proveedores
- Evaluaciones de rendimiento y retroalimentación regulares
Este enfoque ha dado lugar a una red de proveedores altamente capacitados que contribuyen significativamente al éxito y la innovación general de Toyota.
11. Ve y Observa: Entendiendo la Situación de Primera Mano
Resuelve problemas y mejora procesos yendo a la fuente y observando y verificando personalmente los datos en lugar de teorizar en base a lo que otras personas o la pantalla del ordenador te dicen.
Observación directa. Genchi genbutsu, o "ve y observa", es un principio fundamental del Método Toyota que enfatiza la importancia de la observación y comprensión de primera mano. Este enfoque:
- Asegura que las decisiones se basen en hechos reales en lugar de datos reportados
- Fomenta que los gerentes se mantengan conectados con las realidades del trabajo
- Facilita una mejor resolución de problemas y mejora de procesos
Ejemplos de genchi genbutsu en acción:
- Ejecutivos visitando regularmente líneas de producción y instalaciones de proveedores
- Ingenieros pasando tiempo en el taller para entender los procesos de fabricación
- Desarrolladores de productos experimentando productos en condiciones del mundo real
Al practicar consistentemente genchi genbutsu, Toyota mantiene una comprensión profunda de sus procesos, productos y necesidades del cliente, lo que lleva a una toma de decisiones y una innovación más efectivas.
12. Toma de Decisiones por Consenso: Consideración Exhaustiva e Implementación Rápida
No elijas una sola dirección y sigue ese camino hasta que hayas considerado exhaustivamente las alternativas. Cuando hayas elegido, muévete rápidamente pero con cautela por el camino.
Toma de decisiones reflexiva. El enfoque de Toyota hacia la toma de decisiones, conocido como nemawashi, implica construir consenso a través de una consideración exhaustiva de alternativas. Este proceso:
- Asegura que se consideren todas las perspectivas antes de tomar decisiones
- Fomenta la aceptación y el compromiso de todas las partes interesadas
- Conduce a decisiones más robustas y bien fundamentadas
Los elementos clave del proceso de toma de decisiones de Toyota incluyen:
- Recopilación de aportes de todas las partes relevantes
- Consideración de múltiples alternativas antes de elegir un curso de acción
- Uso de herramientas como informes A3 para comunicar claramente las propuestas
- Implementación rápida una vez que se toma una decisión
Si bien este enfoque puede parecer que consume tiempo, en última instancia conduce a una implementación más rápida y efectiva, ya que los problemas potenciales se identifican y abordan temprano en el proceso.
Última actualización:
FAQ
What's The Toyota Way about?
- Management Principles Overview: The Toyota Way by Jeffrey K. Liker outlines 14 management principles that have driven Toyota's success. These principles emphasize long-term philosophy, continuous improvement, and respect for people.
- Cultural Insights: The book explores Toyota's unique culture, highlighting how their success is not just about tools but a comprehensive approach to management and production.
- Practical Applications: It provides insights into applying these principles across various industries, making it relevant beyond automotive manufacturing.
Why should I read The Toyota Way?
- Learn from Success: The book offers a blueprint for achieving operational excellence by understanding Toyota's strategies that have made it a global leader.
- Applicable to Any Business: The principles can be adapted to improve efficiency, quality, and employee engagement in various sectors.
- Cultural Transformation: It provides a framework for transforming organizational culture, essential for long-term success in today's competitive environment.
What are the key takeaways of The Toyota Way?
- Long-Term Philosophy: Emphasizes making management decisions based on long-term goals rather than short-term financial gains, fostering sustainable growth.
- Continuous Improvement: Highlights the importance of kaizen, encouraging all employees to contribute to enhancing processes and products.
- Respect for People: Stresses the importance of respecting employees and fostering a culture of teamwork and empowerment, leading to higher morale and productivity.
What is the Toyota Production System (TPS)?
- Lean Manufacturing Framework: TPS is a lean manufacturing framework focusing on eliminating waste and improving efficiency.
- Key Principles: Built on principles like just-in-time production, jidoka, and continuous flow, creating a responsive and efficient manufacturing environment.
- Cultural Integration: TPS is deeply embedded in Toyota's culture, encouraging employees to take ownership of their work and continuously seek improvements.
How does The Toyota Way define continuous improvement (kaizen)?
- Incremental Changes: Kaizen involves making small, incremental changes to processes over time, allowing organizations to adapt and evolve without major disruptions.
- Employee Involvement: Emphasizes the involvement of all employees in identifying areas for improvement, fostering a sense of ownership and accountability.
- Structured Process: Uses tools like the five-why analysis to identify root causes of problems, ensuring improvements are based on thorough understanding.
What is the concept of genchi genbutsu in The Toyota Way?
- Go and See: Genchi genbutsu translates to "go and see for yourself," emphasizing firsthand observation in understanding problems.
- Deep Understanding: Encourages managers to observe processes in person to gain a deeper understanding and identify root causes of issues.
- Cultural Significance: Promotes a mindset of inquiry and continuous learning, empowering employees to take initiative in problem-solving.
How does The Toyota Way approach employee empowerment?
- Involvement in Decision-Making: Encourages employees to participate in problem-solving and decision-making processes, leading to a sense of ownership.
- Training and Development: Invests in training employees to understand the processes and principles of the Toyota Way, enabling effective contribution.
- Standardized Work: Establishes standardized tasks, providing clear guidelines that empower employees to identify areas for improvement.
What role does leadership play in The Toyota Way?
- Developing Leaders: Stresses the importance of growing leaders who understand the work and embody the Toyota philosophy.
- Consensus Building: Involves building consensus among team members before making decisions, ensuring all perspectives are considered.
- On-the-Floor Engagement: Leaders are expected to spend time on the shop floor, engaging with employees and understanding processes.
How does The Toyota Way address supplier relationships?
- Partnership Approach: Views suppliers as partners and invests in their development, fostering mutual respect and continuous improvement.
- Challenging Suppliers: Challenges suppliers to meet high standards while providing support and resources to help them improve.
- Long-Term Relationships: Focuses on building long-term relationships with suppliers, ensuring stability and quality in the supply chain.
What is the significance of jidoka in The Toyota Way?
- Built-in Quality: Jidoka means "automation with a human touch," allowing machines to stop when a problem occurs, ensuring quality.
- Empowerment: Empowers workers to halt production if they notice defects, fostering a culture of accountability and continuous improvement.
- Immediate Problem-Solving: By stopping the line to address issues, Toyota can quickly identify and resolve problems, preventing defects.
What are the 14 principles of The Toyota Way?
- Long-Term Philosophy: Base management decisions on long-term goals.
- Continuous Process Flow: Create flow to surface problems quickly.
- Pull Systems: Use pull systems to avoid overproduction.
- Level Workload (Heijunka): Level out production to reduce waste.
- Build Quality: Stop to fix problems and ensure quality.
- Standardized Tasks: Standardize work to empower employees and improve processes.
- Visual Control: Use visual management to make problems visible.
- Reliable Technology: Use only tested technology that supports people.
- Grow Leaders: Develop leaders who understand and teach the philosophy.
- Exceptional Teams: Build teams that embody the company’s philosophy.
- Respect Partners: Challenge and help suppliers improve.
- Go and See: Understand situations through direct observation.
- Consensus Decision-Making: Make decisions slowly by consensus.
- Learning Organization: Reflect and improve continuously.
What are the best quotes from The Toyota Way and what do they mean?
- "We place the highest value on actual implementation and taking action.": Emphasizes practical application over theoretical knowledge, reflecting Toyota's belief in learning through doing.
- "If some problem occurs in one-piece flow manufacturing then the whole production line stops.": Highlights the principle of jidoka, ensuring quality by addressing issues immediately.
- "The slower but consistent tortoise causes less waste and is much more desirable than the speedy hare.": Advocates for steady, consistent work over erratic, high-speed production, minimizing waste and maximizing quality.
Reseñas
El Método Toyota recibe grandes elogios por sus valiosas ideas sobre los principios de gestión de Toyota y las técnicas de manufactura esbelta. Los lectores aprecian las aplicaciones prácticas del libro más allá de la simple fabricación, encontrando en él un valor significativo para la mejora empresarial y personal. Los 14 principios se consideran una guía integral para crear una organización eficiente y centrada en la calidad. Algunos lectores mencionan que el libro puede resultar seco o repetitivo, pero la mayoría lo encuentra iluminador y transformador. Muchos expresan un renovado respeto por Toyota y su enfoque tras la lectura.
Similar Books
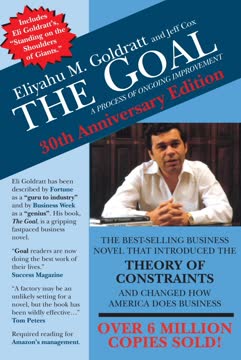
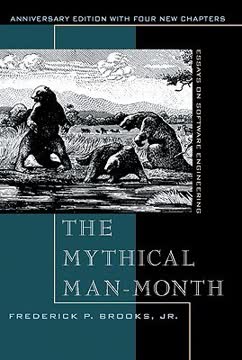
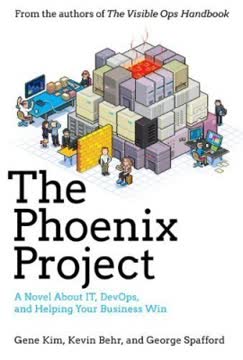
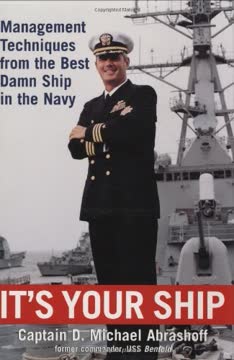
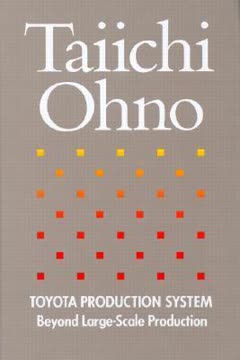
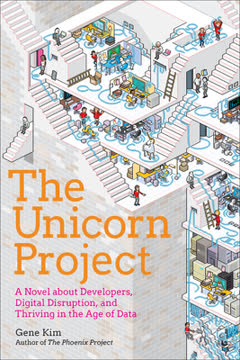
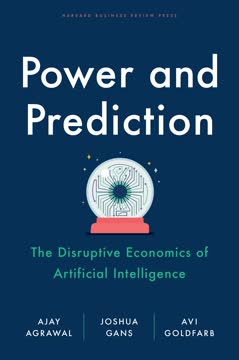
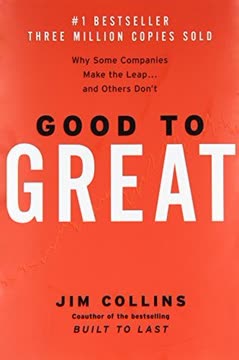