Key Takeaways
1. Lean is Fundamentally Simple, Not Complex Theory
Lean is not as complicated as all the experts and textbooks make it out to be.
Avoid complexity. Many books and consultants make Lean seem like a daunting academic exercise filled with complicated diagrams and jargon. This approach misses the point entirely; Lean is inherently simple and accessible to everyone, regardless of their background or education level. The goal is to make daily life and work easier and more enjoyable, not to create complex systems.
Fun and engaging. Lean should be a fun and exciting process, like a giant scavenger hunt to find and eliminate waste. When Lean is presented as tedious theory, it fails to inspire the passion needed for it to take root and become a sustainable culture. The focus should be on practical application and visible results that motivate people.
Accessible to everyone. This book is intended to blast open the door for anyone wanting to improve their daily life, whether at work or home. Lean thinking, when simplified, can be incorporated by a homemaker or an executive, proving that its principles are universal and not limited to manufacturing theory or business school.
2. Waste is Everywhere (90%) and Learning to See It is the First Step
You and I are 24/7 waste generators.
Identify the 8 wastes. Waste is like gravity, constantly pulling at us and our processes. Recognizing the eight types of waste is crucial because if you can't see waste, you can't eliminate it. These wastes include overproduction, transportation, excess inventory, defects, over-processing, wasted motion, waiting time, and not using employee genius.
Organized waste exists. Many companies and individuals are highly organized, but they are simply organizing waste. Having perfectly labeled shelves of excess inventory is still waste, even if it looks neat. The goal is to eliminate the non-value-added activity entirely, not just make it look pretty.
90% is waste. A staggering amount of what we do daily is non-value-added activity. Simple exercises like charting a "spaghetti trail" of a common task reveal how much time is spent on wasted motion compared to value-added work. Tapping into human potential requires a system to harness this problem-solving genius to eliminate waste.
3. Continuous Improvement Happens Daily, Through Small, 2-Second Steps
Two seconds will change the world!
Lower the bar. Asking for a "2 second improvement" every day makes continuous improvement attainable for everyone. It sets the expectation so low that nobody can fail to meet it, encouraging participation and building momentum. This simple concept is the engine of a vibrant Lean culture.
Daily routine is key. Building time into the workday for improvement, such as the first hour for 3Ss (sweep, sort, standardize), reinforces the expectation. The morning improvement walk inspects this expectation, and celebrating improvements reinforces the behavior. This consistent daily rhythm is more effective than sporadic large events.
Compounding effect works. While 2 seconds seems insignificant, these small daily improvements compound rapidly. People often deliver improvements that save minutes or even hours, far exceeding the initial expectation. This demonstrates the power of making improvement a simple, daily habit rather than a burdensome task.
4. Start Improving by Fixing What Personally Bugs You
Lean is simply fixing what bugs you.
Personal motivation drives change. The easiest way to start seeing and eliminating waste is to focus on the things that personally irritate you in your daily life or work. These frustrations highlight inefficiencies and provide immediate motivation to find a better way. This makes the process relatable and engaging.
Home examples abound. Simple home improvements like adding more light to a closet to see clothes better, combining Splenda and cinnamon to eliminate steps in making tea, or creating a lawn mower bidet to simplify cleaning demonstrate how fixing what bugs you applies everywhere. These small victories are psychologically liberating.
Psychological liberation follows. When you simplify a necessary daily process that used to frustrate you, life gets better quickly. These improvements, no matter how small, reduce hassle, eliminate rework, and free up mental energy. Asking "What bugs me?" daily is a powerful starting point for continuous improvement.
5. Building a Lean Culture Means Focusing on Growing People, Not Just Processes
At its core, Lean is really about the process of growing people.
People over process. Many Lean implementations fail because they focus 90% on process and only 10% on people. World-class Lean companies like Toyota prioritize teaching and training their people and building a culture of continuous improvement. The most important thing is how to build people and a culture, not just optimize a process.
Motivation matters. As a leader, you might be motivated by business growth, but employees are motivated by good jobs, paychecks, satisfaction, and camaraderie. To make Lean stick, you must align Lean with their motivations by showing them how it improves their work life and provides personal growth opportunities.
Culture makes it stick. Lean is not about conducting Lean "events"; it's about building a culture where continuous improvement is a natural way of thinking. This requires consistent investment in teaching and training, making people feel valued, and empowering them to be problem-solvers.
6. Key Practices for Culture: Daily Morning Meeting & Improvement Walk
The number one thing that people want in life is to feel that their ideas matter and they are making a difference.
Morning meeting routine. A short daily morning meeting is the cornerstone of building a Lean culture. It provides a consistent time to review mistakes and improvements, discuss sales, share company principles, and engage in continuous learning by reading relevant books together. This aligns everyone's perspective.
Improvement walk reinforces. Following the meeting with a morning walk where leaders check on daily improvements reinforces the expectation. Asking employees "What's your improvement for today?" shows that improvement is a priority and provides opportunities to coach and celebrate progress. This makes improvement visible and accountable.
Building leaders daily. Rotating the leadership of the morning meeting among employees, even those who are shy, builds confidence and leadership skills. This practice demonstrates trust in people and empowers them to take ownership of the culture, showing them their value extends beyond their specific job tasks.
7. Document Improvements with Simple "Before & After" Videos (Third Pillar)
The Third Pillar of Lean is…you must make “before and after” videos of all your improvements.
Visualize the change. Making simple "before and after" videos of improvements is a critical pillar of Lean culture. It clearly documents progress, makes the impact of improvements visible to everyone, and creates a library of success stories. This adds emotional energy and makes Lean fun and engaging.
Simple tools suffice. You don't need expensive equipment; use the phone in your pocket and simple editing apps. The goal is to capture the change easily and quickly, not to produce Hollywood films. Overcomplicating the process can lead to paralysis, as the author experienced initially.
Teaching and sharing. These videos serve as powerful teaching tools for current and future employees, showing them what improvements look like in practice. Sharing them externally, like on a website, allows others to learn and provides employees with a sense of pride that their work is influencing people globally.
8. Standardize and Simplify Everything, Starting with the Bathroom (3Ss)
LEAN STARTS IN THE BATHROOM.
Create a visual standard. The bathroom is a perfect place to start implementing Lean because it's a shared experience everyone uses multiple times a day. Making all bathrooms identical, clean, and well-stocked with standardized supplies creates a clear, visual standard for what Lean looks like throughout the facility.
Implement the 3Ss. The basic principles of sweep, sort, and standardize are easily applied to the bathroom. Cleaning the area (sweep), removing unnecessary items (sort), and using the same products and checklist in every bathroom (standardize) makes the process simple and predictable. This allows anyone to clean it perfectly.
Respect for people. A clean, standardized bathroom demonstrates respect for everyone who uses it. Leaving it better than you found it is a simple act of courtesy that reinforces the culture of respect. Standardizing mundane tasks frees up mental energy for higher-level thinking and continuous improvement.
9. Lean Leadership Requires Humility, Trust, and Deflecting Credit
HUMILITY IS THE PATH TO GREATNESS.
Validate and appreciate. A humble Lean leader actively seeks ideas from everyone and consistently validates, compliments, and recognizes employees' contributions. Saying things like "That's a great idea" or "I like your idea better than mine" builds trust and encourages people to share their genius without fear of ego or politics.
Trust allows growth. Leaders must trust their people enough to let them make mistakes. Failure is a powerful learning opportunity, and robbing employees of this experience stifles innovation. Trusting people to find and implement improvements, even small ones, unleashes their potential and makes them better problem-solvers.
Deflect credit always. Deflecting credit away from yourself and giving it to others is a strategic leadership trait. When leaders model this generosity, it fosters a collaborative culture where people are eager to help each other and share credit. This creates a positive environment where everyone feels valued and motivated.
10. Lean is Hard Work That Ultimately Makes Everything Easy
Lean is hard work that makes everything easy.
Counterintuitive effort pays off. Implementing Lean requires initial effort and discipline, which can feel like hard work, especially when busy. However, consistently applying Lean principles, like stopping to improve even when the workload is high, ultimately makes processes smoother, faster, and less burdensome. This leads to increased productivity and reduced stress.
Eliminate struggle for flow. The goal of Lean is "zero struggle" in every activity. This means eliminating burden (Muri), unevenness (Mura), and waste (Muda). By removing these obstacles through continuous improvement, work flows naturally, making tasks feel easy and enjoyable, even complex ones.
Increased productivity follows. When work flows smoothly and people enjoy their tasks, productivity increases dramatically. Companies that prioritize Lean can achieve significantly more with the same or fewer resources, often eliminating the need for overtime. This efficiency is a direct result of the initial hard work invested in improvement.
11. Focus on Eliminating Your Own Waste Before Pointing Out Others'
Focus on yourself.
Enough waste for a lifetime. Everyone has more than enough waste in their own life and work processes to focus on. Pointing out others' waste is unproductive and can create defensiveness. The most effective approach is to focus relentlessly on improving your own area of influence.
Lead by example. When others see the positive results of your Lean efforts – how much easier your work is, how much more reliable you are, how the quality of your output improves – they will become curious and want to learn from you. Your results will be the most compelling argument for Lean thinking.
Mature culture asks. A sign of a mature Lean culture is when people are comfortable asking "Where is my waste?" or "What do I need to improve?" This self-reflective approach, modeled by leadership, fosters a continuous learning environment where everyone is focused on personal and process improvement.
12. The True Reward of Lean Comes From Giving Back and Helping Others
GIVING IS GREATER THAN RECEIVING
Serve others first. The real "juice" of Lean comes when an organization focuses on serving others – customers, employees, and the community – rather than just maximizing profit. Profit becomes a byproduct of excellence in serving and improving the lives of people.
Giving back amplifies Lean. Teaching and training others outside your organization, giving tours, and sharing your Lean journey amplifies your own learning. New eyes looking at your processes reveal more opportunities for improvement. This act of giving back strengthens your own culture and spreads the benefits of Lean.
Purpose over profit. Companies driven by a purpose beyond just making money, like improving humanity or making the world better, build more dynamic and sustainable Lean cultures. This focus on contribution motivates employees and creates a positive environment where everyone feels they are making a difference.
Last updated:
Review Summary
2 Second Lean receives mixed reviews, with an average rating of 3.95 out of 5. Many readers praise its simplicity, practicality, and enthusiasm in explaining lean principles for everyday life and business. The book's key message of making small, continuous improvements resonates with many. However, some criticize it for being repetitive, overly self-promotional, and lacking depth. While some find it inspiring and applicable, others feel it oversimplifies complex concepts. The audiobook version is particularly recommended for the author's infectious enthusiasm.
Similar Books
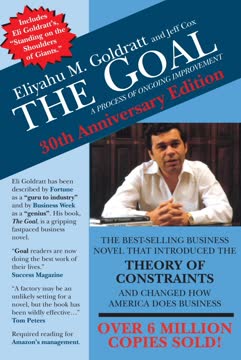
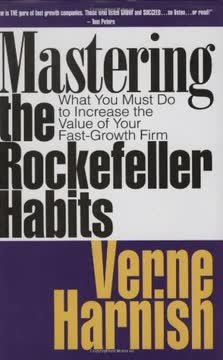
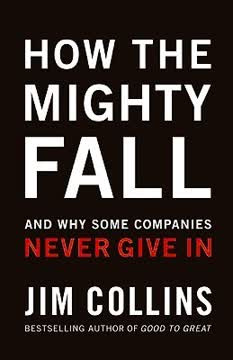
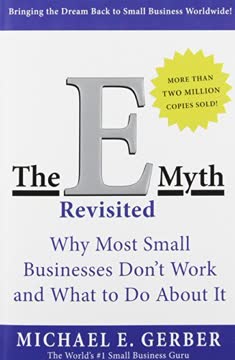
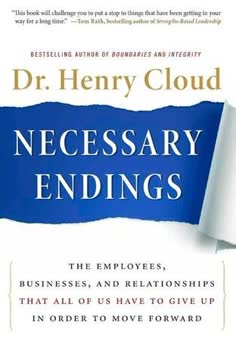
Download PDF
Download EPUB
.epub
digital book format is ideal for reading ebooks on phones, tablets, and e-readers.