Key Takeaways
1. Inventory is both a physical and financial asset
Inventory brings with it a number of costs. These costs can include: Dollars, Space, Labor to receive, check quality, put away, retrieve, select, pack, ship, and account for, Deterioration, damage, and obsolescence, Theft
Dual nature of inventory. Inventory exists simultaneously as physical goods and financial records. This duality creates challenges in tracking and valuing stock. Physically, inventory occupies space and requires labor to handle. Financially, it ties up capital and impacts financial statements.
Costs beyond purchase price. The true cost of inventory extends far beyond the initial purchase price:
- Carrying costs (storage, insurance, taxes)
- Handling costs (receiving, moving, shipping)
- Obsolescence and spoilage
- Opportunity cost of tied-up capital
Financial impact. Inventory directly affects key financial metrics:
- Balance sheet: Listed as a current asset
- Income statement: Impacts cost of goods sold and profitability
- Cash flow: Large inventories can strain working capital
2. Effective inventory management balances carrying costs and replenishment costs
The closer the K Factor and the R Factor are to being equal, the more likely you are to have the correct amount of product at the overall lowest cost.
Balancing act. Optimal inventory management requires finding the sweet spot between holding too much stock (high carrying costs) and ordering too frequently (high replenishment costs).
Key factors:
- K Factor: Carrying cost per dollar of inventory per year
- R Factor: Cost per purchase order line item
Economic Order Quantity (EOQ). This formula helps determine the optimal order size by balancing carrying and ordering costs:
EOQ = √((2 * Annual Demand * Order Cost) / (Unit Cost * Carrying Cost %))
Considerations:
- Higher order quantities: Lower ordering costs, higher carrying costs
- Lower order quantities: Higher ordering costs, lower carrying costs
- Industry and product characteristics influence the optimal balance
3. Locator systems and placement strategies optimize warehouse efficiency
The purpose of a material locator system is to create procedures that allow you to track product movement throughout the facility.
Types of locator systems:
- Memory systems: Rely on human recall, suitable for small operations
- Fixed location: Each item has a designated spot
- Random location: Items stored wherever space is available
- Zoning: Similar items grouped together
- Combination: Blends multiple approaches
Placement strategies:
- ABC analysis: Categorize items based on value or usage
- Family grouping: Store related items together
- Special considerations: Account for size, weight, or handling requirements
Optimization techniques:
- Minimize travel time for high-volume items
- Balance accessibility and space utilization
- Use technology (e.g., barcodes, RFID) to track locations
4. Bar coding revolutionizes inventory tracking and accuracy
The speed of information capture and the accuracy of bar coding are often sufficient reasons to cost justify installing bar coding within your operation.
Benefits of barcoding:
- Drastically reduces data entry errors
- Increases speed of inventory transactions
- Enables real-time tracking of stock levels
- Improves accuracy of picking and shipping
Key components:
- Barcode symbology (e.g., UPC, Code 39, QR codes)
- Scanning devices (handheld, fixed-mount, mobile computers)
- Printing technology (thermal, laser, inkjet)
Implementation considerations:
- Choose appropriate symbology for your needs
- Integrate with existing inventory management software
- Train staff on proper scanning and equipment maintenance
- Develop standard operating procedures for barcode use
5. Forecasting and replenishment methods vary based on demand patterns
Independent demand calls for a replenishment approach to inventory management. This approach assumes that market forces will exhibit a somewhat fixed pattern.
Independent vs. Dependent Demand:
- Independent: Finished goods, influenced by market forces
- Dependent: Raw materials and components, driven by production schedules
Forecasting methods:
- Time series analysis (e.g., moving averages, exponential smoothing)
- Causal methods (e.g., regression analysis)
- Qualitative techniques (e.g., Delphi method, market research)
Replenishment systems:
- Reorder Point (ROP): Order when inventory reaches a predetermined level
- Periodic Review: Check inventory at fixed intervals and order to reach target level
- Min-Max: Maintain inventory between minimum and maximum levels
Advanced techniques:
- Material Requirements Planning (MRP) for dependent demand
- Just-In-Time (JIT) for minimizing inventory and waste
- Vendor-Managed Inventory (VMI) for supply chain collaboration
6. Cycle counting is key to maintaining inventory accuracy
Cycle counting is simply counting a statistically significant cross-section of your inventory frequently.
Benefits of cycle counting:
- Identifies discrepancies quickly
- Maintains ongoing accuracy without disrupting operations
- Reduces or eliminates need for annual physical inventory
- Improves understanding of inventory processes and problems
Cycle counting methods:
- ABC analysis: Count high-value items more frequently
- Random sampling: Select items to count randomly
- Geographic: Count all items in a specific location
- Process-based: Count items involved in specific transactions
Best practices:
- Establish clear procedures and documentation
- Train counters thoroughly
- Investigate and resolve discrepancies promptly
- Use technology (e.g., mobile devices, barcode scanners) to streamline counting
- Analyze results to identify patterns and improve processes
7. Emergency planning and theft prevention protect inventory assets
Business emergencies are a question of "when," not "if."
Emergency preparedness:
- Assess potential risks (natural disasters, power outages, etc.)
- Develop detailed response plans
- Train staff on emergency procedures
- Regularly review and update plans
- Implement backup systems for critical data and operations
Theft prevention strategies:
- Physical security measures (locks, alarms, cameras)
- Access control systems
- Employee screening and background checks
- Inventory tracking and regular audits
- Security awareness training for all staff
Crime Prevention Through Environmental Design (CPTED):
- Natural surveillance: Design spaces to maximize visibility
- Access control: Guide movement and limit entry points
- Territorial reinforcement: Clearly define public and private areas
- Maintenance: Keep facilities well-maintained to deter criminal activity
Inventory insurance:
- Review coverage regularly
- Understand policy limits and exclusions
- Consider business interruption insurance
- Document inventory thoroughly for potential claims
Last updated:
Review Summary
Essentials of Inventory Management receives mixed reviews, with an average rating of 3.69/5. Readers appreciate its comprehensive coverage of inventory management basics, making it suitable for beginners and those in purchasing, warehousing, or logistics. The book's clear narration and problem-solving approach are praised. However, some criticize its outdated examples and lack of focus on modern, lean supply chain practices. Despite this, many find it a solid primer on inventory management essentials, covering topics from classification to procurement and cycle counting.
Similar Books
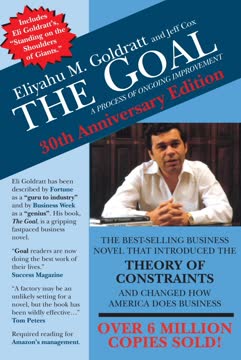
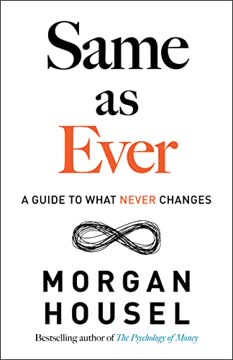
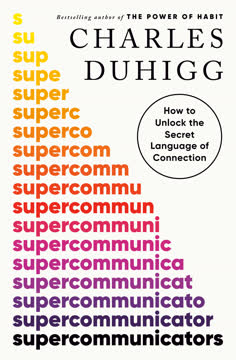
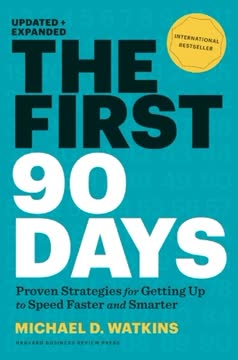
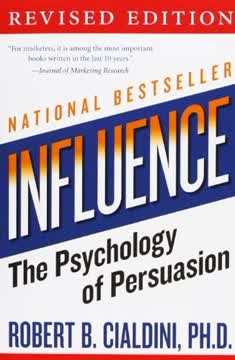
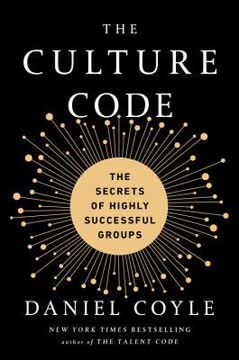
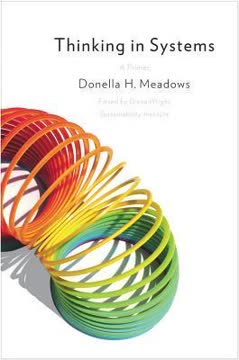
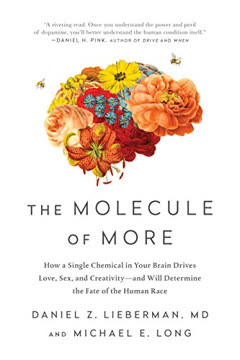
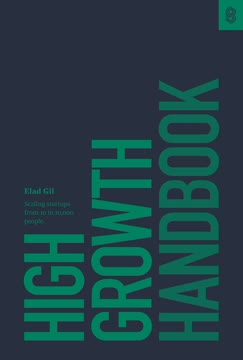
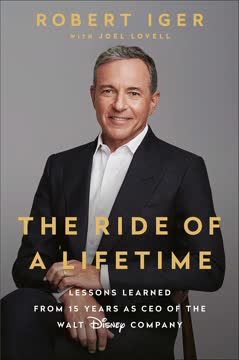
Download PDF
Download EPUB
.epub
digital book format is ideal for reading ebooks on phones, tablets, and e-readers.