Key Takeaways
1. Lean manufacturing starts with customer satisfaction and delivery
"Remember that delivery comes first, then reduce inventory, and finally worry about cost."
Customer satisfaction is paramount. Lean manufacturing begins with understanding and meeting customer needs. This means prioritizing on-time delivery, product quality, and cost-effectiveness in that order.
- Focus on:
- Delivering products on time
- Reducing inventory
- Optimizing costs
By prioritizing delivery, companies ensure customer satisfaction while building trust and loyalty. Reducing inventory helps identify inefficiencies in the production process and frees up working capital. Only after these two aspects are addressed should companies focus on cost reduction, ensuring that cost-cutting measures don't negatively impact delivery or quality.
2. Visualize the value stream to identify waste and improve flow
"Gold flows through the factory. There's gold in these people's hands. Our job is to find it."
Value Stream Mapping (VSM) is a powerful tool for visualizing the entire production process. It helps identify areas of waste and opportunities for improvement in both material and information flows.
Key components of VSM:
- Material flow: How products move through the production process
- Information flow: How orders and production instructions are communicated
- Timeline: Total lead time and value-added time
By creating a visual representation of the entire process, managers can easily spot bottlenecks, excessive inventory, and non-value-added activities. This "treasure map" guides improvement efforts, allowing teams to focus on areas that will have the most significant impact on overall efficiency and flow.
3. Implement pull systems and kanban to reduce inventory and improve efficiency
"Produce what has been consumed in the same quantity and the same order."
Pull systems and kanban are fundamental lean tools that help regulate production based on actual customer demand. This approach minimizes overproduction and reduces inventory throughout the value stream.
Key aspects of pull systems:
- Kanban cards or signals trigger production
- Work is only performed when there's a downstream demand
- Production is limited to replenishing what has been consumed
Implementing pull systems requires a shift in mindset from traditional push production. It may initially feel counterintuitive, but it leads to smoother flow, reduced inventory, and improved responsiveness to customer needs.
4. Standardize work and implement kaizen for continuous improvement
"Kaizen is not just about cost reduction, it's about developing people."
Standardized work provides a baseline for improvement, while kaizen (continuous improvement) drives ongoing refinement of processes. Together, they create a cycle of stability and innovation.
Standardized work:
- Defines the current best practice
- Reduces variation in processes
- Provides a foundation for training
Kaizen:
- Engages employees in problem-solving
- Identifies and eliminates waste
- Continuously improves processes
By standardizing work and engaging employees in continuous improvement, organizations can create a culture of learning and innovation that drives ongoing performance gains.
5. Develop people before producing parts
"Produce people before you produce parts."
People development is crucial for sustainable lean implementation. Investing in employee skills, knowledge, and problem-solving abilities creates a workforce capable of driving continuous improvement.
Key aspects of people development:
- On-the-job training
- Cross-functional skill building
- Problem-solving techniques
- Leadership development
By prioritizing people development, organizations create a workforce that is adaptable, engaged, and capable of sustaining lean improvements over time. This approach recognizes that employees are the most valuable asset in driving long-term success.
6. Create a culture of problem-solving and continuous learning
"Never bypass a problem, and then kaizen."
Problem-solving culture is essential for lean success. Encouraging employees to identify and address problems as they arise fosters a mindset of continuous improvement and learning.
Elements of a problem-solving culture:
- Encourage problem identification
- Use structured problem-solving methods (e.g., A3, 5 Whys)
- Celebrate learning from failures
- Share knowledge across the organization
By creating an environment where problems are seen as opportunities for improvement, organizations can tap into the collective intelligence of their workforce and drive ongoing innovation.
7. Leadership is key to sustaining lean transformation
"Running a business is about running a business, period."
Strong leadership is crucial for sustaining lean transformation. Leaders must be actively involved in the lean journey, modeling desired behaviors and supporting the cultural change required for success.
Leadership responsibilities in lean:
- Set clear vision and goals
- Allocate resources for improvement
- Remove obstacles to change
- Develop future leaders
- Maintain focus on long-term success
Effective lean leaders balance short-term results with long-term capability building, ensuring that the organization continues to improve and adapt over time.
8. Balance flexibility and stability in production
"The Toyota rule is to invest 10% of production time in flexibility."
Flexibility and stability are both essential in lean production. While standardization provides stability, organizations must also build in flexibility to respond to changing customer demands.
Balancing flexibility and stability:
- Implement quick changeover techniques (SMED)
- Cross-train employees
- Design flexible production cells
- Use heijunka (production leveling) to smooth demand
By investing in both stability and flexibility, organizations can create robust production systems capable of meeting diverse customer needs while maintaining efficiency.
9. Use visual management and gemba walks to stay connected to the process
"Gemba attitude means that you make every decision based on the principle that real improvement only takes place through a shop-floor focus based on direct observation."
Visual management and gemba walks keep leaders and managers connected to the actual work processes. These practices promote better decision-making and more effective problem-solving.
Visual management tools:
- Production boards
- Andon lights
- Kanban cards
- 5S workplace organization
Gemba walks:
- Regular visits to the work area
- Direct observation of processes
- Conversations with frontline employees
- Immediate problem-solving
By staying connected to the gemba (the actual place where work is done), leaders can make more informed decisions and provide better support to their teams.
10. Implement heijunka (production leveling) to smooth demand fluctuations
"Following the heijunka way is about avoiding peaks and valleys."
Heijunka helps organizations balance production and smooth out demand fluctuations. This approach reduces the strain on resources and helps maintain a consistent flow of work.
Benefits of heijunka:
- Reduced inventory
- More stable workforce utilization
- Improved supplier relationships
- Enhanced ability to meet customer demand
Implementing heijunka requires careful planning and coordination across the entire value stream. It may involve strategies such as:
- Mixed model production
- Smaller, more frequent production runs
- Closer collaboration with customers and suppliers
By leveling production, organizations can create more stable and efficient processes that are better equipped to handle variations in customer demand.
Last updated:
FAQ
What's The Gold Mine: A Novel of Lean Turnaround about?
- Lean Management Focus: The book is a novel that illustrates lean management principles through a fictional narrative. It follows Philip Jenkinson's journey as he attempts to save his manufacturing company from financial crisis with the help of his friend Mike and Mike's father, Bob Woods.
- Human Element: It emphasizes that successful lean transformations require understanding and managing people, not just technical skills. The story showcases the challenges and dynamics of implementing lean practices in a real-world setting.
- Practical Lessons: Characters learn about key lean concepts such as takt time, standardized work, and waste reduction, making it a practical guide for managers and leaders.
Why should I read The Gold Mine?
- Engaging Storytelling: The novel format makes complex lean concepts accessible and relatable, allowing readers to learn through character experiences rather than dry theory.
- Real-World Application: It provides practical insights into lean management that can be applied across various industries, helping readers implement lean principles effectively in their organizations.
- Inspiration for Leaders: The book serves as a motivational tool for managers and leaders, encouraging them to embrace lean thinking and foster a culture of continuous improvement.
What are the key takeaways of The Gold Mine?
- People-Centric Approach: Lean management is fundamentally about people and their involvement in the process. Engaging employees in decision-making and problem-solving is crucial for successful implementation.
- Continuous Improvement: Concepts like kaizen and standardized work are highlighted as essential for reducing waste and improving efficiency. The focus is on small, incremental changes that lead to significant results over time.
- Takt Time Importance: Understanding and applying takt time is crucial for aligning production with customer demand, helping manage workflow effectively.
What is takt time, as defined in The Gold Mine?
- Definition: Takt time is the maximum allowable time to produce a product to meet customer demand, calculated by dividing available production time by required output.
- Production Rhythm: It establishes a rhythm for production, ensuring products are made at a pace that matches customer needs, preventing overproduction and excess inventory.
- Operational Efficiency: Adhering to takt time helps streamline processes, reduce waste, and improve overall efficiency, serving as a critical metric for managing production flow.
How does The Gold Mine illustrate the concept of waste?
- Seven Types of Waste: The book identifies seven types of waste in manufacturing: overproduction, waiting, excess transport, overprocessing, unnecessary inventory, unnecessary motion, and defects.
- Real-World Examples: Characters encounter various forms of waste, such as excess inventory and waiting times, which hinder productivity. The narrative demonstrates how addressing these wastes can lead to significant improvements.
- Lean Mindset: The story encourages a lean mindset where employees are trained to identify and eliminate waste in their daily tasks, essential for long-term success in lean transformations.
What is standardized work in The Gold Mine?
- Definition: Standardized work involves establishing precise procedures for each task to ensure consistency and quality, defining the best way to perform a job based on efficient methods.
- Benefits: It helps reduce variation in processes, leading to improved quality and efficiency, allowing operators to perform tasks predictably, minimizing errors and rework.
- Operator Involvement: The book emphasizes that standardized work should be developed with input from operators, fostering ownership and commitment to the process.
What is the concept of jidoka in The Gold Mine?
- Automation with Human Touch: Jidoka refers to machines' ability to stop automatically when a defect is detected, ensuring quality issues are addressed immediately.
- Empowerment of Workers: It encourages operators to take responsibility for quality, allowing them to halt production if they notice a problem, fostering a culture of accountability.
- Focus on Quality: The principle reinforces that quality must be built into the process rather than inspected at the end, reducing waste and improving overall efficiency.
How does The Gold Mine define kaizen?
- Continuous Improvement Philosophy: Kaizen is described as a philosophy of continuous, incremental improvement in all aspects of life and work, not just manufacturing.
- Employee Involvement: The book stresses that kaizen requires the involvement of all employees, encouraging them to identify problems and suggest solutions.
- Structured Approach: It outlines a structured approach to kaizen, including the use of standardized work and regular reviews to assess progress and make adjustments.
What is the lake and rocks analogy in The Gold Mine?
- Visualizing Waste: The analogy compares inventory (the lake) to inefficiencies (the rocks) hidden beneath the surface. Reducing inventory reveals these inefficiencies, prompting action to eliminate them.
- Encouraging Problem-Solving: By lowering inventory levels, organizations can surface problems that need addressing, fostering a culture of continuous improvement.
- Practical Application: This concept encourages managers to focus on reducing waste and improving processes rather than simply increasing production capacity.
What role does leadership play in The Gold Mine?
- Driving Change: Effective leadership is essential for guiding teams through lean transformation challenges and fostering a culture of continuous improvement.
- Empowering Employees: Leaders must empower employees to take ownership of their work and encourage them to contribute to problem-solving and innovation.
- Building Trust: The book emphasizes the need for leaders to build trust within their teams, crucial for successful collaboration and engagement in lean initiatives.
What are the best quotes from The Gold Mine and what do they mean?
- “It’s all about the people.”: This quote encapsulates the book's central theme that successful lean transformations depend on understanding and managing human behavior, not just technical processes.
- “Gold in the flow.”: This phrase highlights the idea that value is created in the production process, and identifying and optimizing the flow of work is essential for achieving efficiency and profitability.
- “Zero defects accepted.”: This quote emphasizes the importance of quality control at every stage of production, encouraging operators to take responsibility for their work and reject defective parts before they move downstream.
How can I apply the lessons from The Gold Mine to my own organization?
- Assess Current Processes: Begin by evaluating your organization's current processes to identify areas of waste and inefficiency. Use concepts like takt time and standardized work to establish a baseline for improvement.
- Engage Employees: Involve your employees in the improvement process by encouraging them to share their insights and suggestions. Create a culture of continuous improvement where everyone feels responsible for quality and efficiency.
- Implement Lean Tools: Apply lean tools and techniques, such as 5S and kaizen, to streamline operations and reduce waste. Monitor progress regularly and adjust strategies as needed to ensure ongoing success.
Review Summary
The Gold Mine receives mostly positive reviews, with readers praising its effective portrayal of lean manufacturing principles through a fictional narrative. Many find it an engaging and accessible introduction to lean concepts, appreciating the blend of business insights and storytelling. Some readers note it's particularly useful for those in manufacturing or management roles. While a few criticize the writing style or find certain aspects confusing, most agree it's a valuable resource for understanding lean transformation and its practical application in business settings.
Similar Books
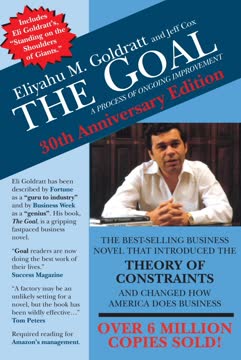
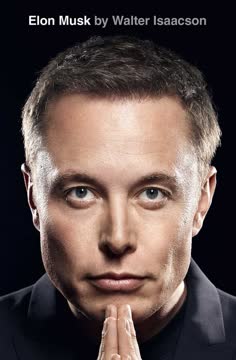
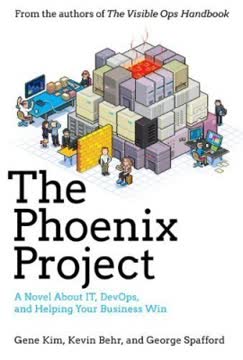
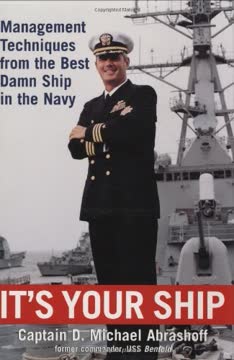
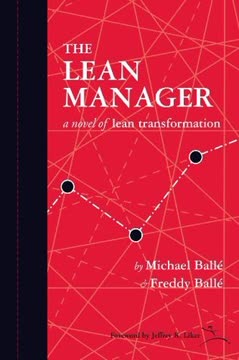
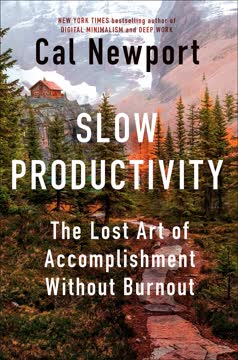
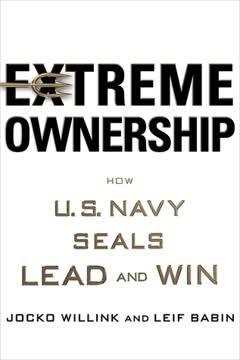
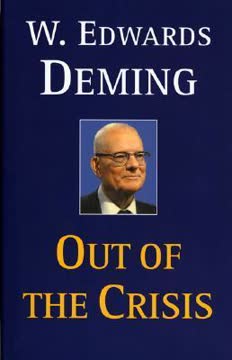
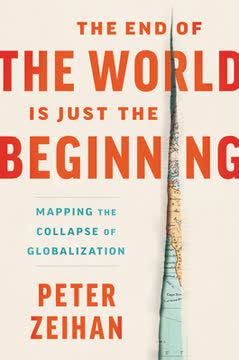
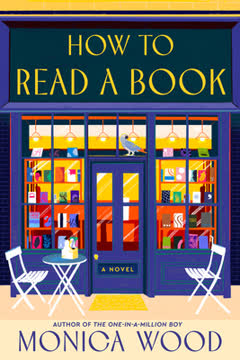
Download PDF
Download EPUB
.epub
digital book format is ideal for reading ebooks on phones, tablets, and e-readers.