Key Takeaways
1. Six Sigma: A Powerful Strategy for Sustained Business Success
Six Sigma is a comprehensive and flexible system for achieving, sustaining and maximizing business success.
Driving organizational excellence. Six Sigma is a data-driven methodology that aims to reduce defects and variations in processes to achieve near-perfect quality. It combines statistical analysis with a focus on customer needs and continuous improvement. By implementing Six Sigma, organizations can:
- Reduce costs and increase profits
- Improve customer satisfaction and loyalty
- Enhance operational efficiency and effectiveness
- Foster a culture of continuous improvement
Proven track record. Companies like Motorola, General Electric, and AlliedSignal have achieved significant results through Six Sigma:
- Motorola: Saved $14 billion over 10 years
- GE: Generated $2 billion in savings within two years
- AlliedSignal: Increased productivity by 6% annually
2. Understanding Process Variation and Customer Focus
Variation in products and services is a critical concern, as it can lead to customer dissatisfaction and increased costs.
Reducing variation. Six Sigma aims to minimize process variation to achieve consistent, high-quality outputs. This is measured using the sigma scale, where Six Sigma equates to 3.4 defects per million opportunities (DPMO).
- 3 Sigma: 66,807 DPMO (93.3% accuracy)
- 4 Sigma: 6,210 DPMO (99.38% accuracy)
- 5 Sigma: 233 DPMO (99.977% accuracy)
- 6 Sigma: 3.4 DPMO (99.99966% accuracy)
Customer-centric approach. Six Sigma emphasizes understanding and meeting customer requirements. This involves:
- Identifying critical-to-quality (CTQ) characteristics
- Developing clear, measurable performance standards
- Continuously gathering and analyzing customer feedback
By focusing on reducing variation and meeting customer needs, organizations can significantly improve their products, services, and overall performance.
3. The DMAIC Model: Define, Measure, Analyze, Improve, Control
DMAIC is grounded in the original Plan-Do-Check-Act cycle; however, we will be using DMAIC to apply to both Process Improvement and Process Design/Redesign efforts.
Structured problem-solving. The DMAIC model provides a systematic approach to process improvement:
- Define: Clearly state the problem, goal, and scope of the project
- Measure: Collect baseline data on current process performance
- Analyze: Identify root causes of problems and variation
- Improve: Develop, test, and implement solutions
- Control: Establish mechanisms to sustain improvements
Versatile application. DMAIC can be used for both incremental process improvements and more radical process redesigns. Key tools and techniques used in each phase include:
- Define: Project charter, SIPOC diagram, Voice of the Customer
- Measure: Data collection plan, Process capability analysis, Pareto charts
- Analyze: Root cause analysis, Fishbone diagrams, Hypothesis testing
- Improve: Solution selection matrix, Pilot testing, Implementation planning
- Control: Control charts, Standard Operating Procedures, Training plans
4. Implementing Six Sigma: Roles, Training, and Project Selection
The key to success you may achieve are broad because the proven benefits of the Six Sigma "system" are diverse, including cost reduction, productivity improvement, market-share growth, customer retention, cycle-time reduction, defect reduction, culture change, and product/service development.
Organizational structure. Successful Six Sigma implementation requires a clear structure of roles and responsibilities:
- Executive Leadership: Provide vision, resources, and accountability
- Champions/Sponsors: Guide projects and remove obstacles
- Master Black Belts: Serve as expert coaches and mentors
- Black Belts: Lead improvement projects full-time
- Green Belts: Support projects part-time while maintaining regular duties
Comprehensive training. Six Sigma requires a significant investment in training to build the necessary skills and knowledge:
- Executive overview (1-2 days)
- Champion training (2-3 days)
- Black Belt training (4-5 weeks, spread over several months)
- Green Belt training (1-2 weeks)
Strategic project selection. Choosing the right projects is crucial for Six Sigma success. Criteria for selection include:
- Alignment with business objectives
- Potential financial impact
- Feasibility and resources required
- Customer impact and satisfaction
- Urgency and timeline
5. Voice of the Customer: Defining and Measuring Requirements
Avoiding the squeaky wheel syndrome is key in Voice of the Customer systems.
Customer-driven quality. Six Sigma emphasizes understanding and meeting customer needs through:
- Identifying key customers and their requirements
- Translating customer needs into measurable specifications
- Continuously gathering and analyzing customer feedback
Multi-faceted approach. Effective Voice of the Customer (VOC) systems employ various methods:
- Surveys and focus groups
- Customer complaints and feedback
- Direct observation and interviews
- Social media and online reviews
- Sales and customer service data
Balanced perspective. Avoid focusing solely on the loudest complaints or most vocal customers. Instead, strive for a representative sample of customer voices, including:
- Current satisfied and dissatisfied customers
- Lost customers
- Competitors' customers
- Potential new customers
By systematically capturing and analyzing customer requirements, organizations can align their processes and outputs with customer expectations, leading to improved satisfaction and loyalty.
6. Process Improvement: Analyzing Root Causes and Implementing Solutions
As long as you and your business leaders recognize that Six Sigma is a way to create and run a more successful organization—demanding a great diversity of skills, not just technical expertise—you can avoid this problem.
Data-driven decision making. Six Sigma process improvement relies on a systematic approach to problem-solving:
- Define the problem and project goals
- Measure current process performance
- Analyze data to identify root causes
- Improve the process by implementing solutions
- Control the improved process to sustain gains
Tools and techniques. Key analytical methods used in Six Sigma include:
- Pareto charts: Identify the vital few causes of problems
- Fishbone diagrams: Visualize potential root causes
- Statistical process control: Monitor and control process variation
- Design of Experiments: Optimize process parameters
Implementing solutions. Successful improvement projects follow these steps:
- Generate multiple potential solutions
- Evaluate and select the best solution(s)
- Develop an implementation plan
- Pilot test the solution
- Full-scale implementation and monitoring
By following this structured approach and using data-driven tools, organizations can effectively identify and address the root causes of problems, leading to significant and sustainable improvements.
7. Process Design/Redesign: Creating New or Overhauling Existing Processes
Process Design/Redesign is sometimes needed to jolt the people and the assumptions that govern an organization out of their reverie that things are just fine the way they are.
Transformative change. Process design/redesign aims to create entirely new processes or radically overhaul existing ones to achieve breakthrough performance improvements. This approach is used when:
- Incremental improvements are insufficient
- New technologies or market conditions demand significant changes
- Existing processes are fundamentally flawed or outdated
Design principles. Key considerations in process design/redesign include:
- Customer focus: Align the process with customer needs and expectations
- Simplification: Eliminate non-value-added steps and complexity
- Standardization: Create consistent, repeatable processes
- Error-proofing: Build in mechanisms to prevent defects
- Technology enablement: Leverage appropriate technologies to improve efficiency
Implementation challenges. Successful process design/redesign requires:
- Strong leadership support and commitment
- Cross-functional collaboration and buy-in
- Effective change management and communication
- Adequate resources and training
- Ongoing monitoring and refinement
By rethinking processes from the ground up, organizations can achieve dramatic improvements in performance, customer satisfaction, and competitive advantage.
8. Overcoming Resistance and Sustaining Six Sigma Efforts
Six Sigma is based in large measure on creating a closed-loop business system that is sensitive enough to reduce the company's "wobbling" and keep it safely on the often-twisted path to performance and success.
Change management. Implementing Six Sigma often requires significant organizational and cultural changes. To overcome resistance:
- Communicate the vision and benefits clearly
- Involve employees at all levels in the change process
- Provide adequate training and support
- Celebrate early wins and share success stories
- Address concerns and fears openly and honestly
Sustaining momentum. To ensure long-term success with Six Sigma:
- Integrate Six Sigma into daily operations and decision-making
- Align rewards and recognition with Six Sigma goals
- Continuously develop new Six Sigma talent and leaders
- Regularly review and refresh Six Sigma efforts
- Foster a culture of continuous improvement and innovation
Measuring success. Track and communicate Six Sigma results using:
- Financial impacts (cost savings, revenue growth)
- Customer satisfaction and loyalty metrics
- Process performance indicators (cycle time, defect rates)
- Employee engagement and cultural change measures
By effectively managing change and sustaining Six Sigma efforts, organizations can create a continuous improvement culture that drives ongoing success and competitiveness.
Last updated:
Review Summary
The Six Sigma Way receives mixed reviews, with an average rating of 3.63 out of 5. Some readers find it informative and comprehensive, praising its practical approach and integration of Six Sigma concepts. Others criticize it for being dry, textbook-like, and lacking in-depth information. Positive reviews highlight the book's usefulness as a reference and training material, while negative reviews express disappointment in its content and presentation. Many readers appreciate the overview of Six Sigma principles but find the material dated or too general for advanced practitioners.
Similar Books
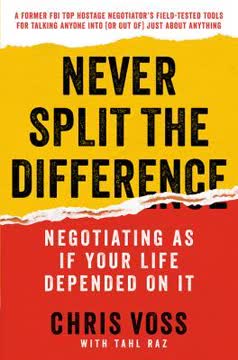
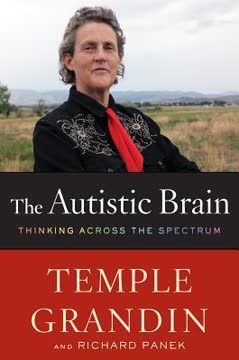
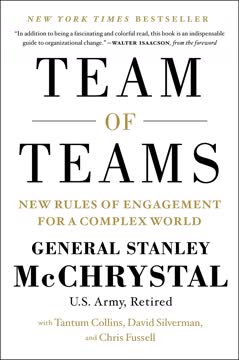
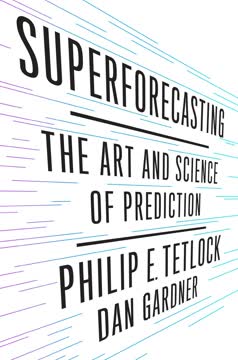
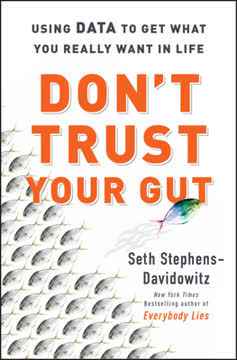
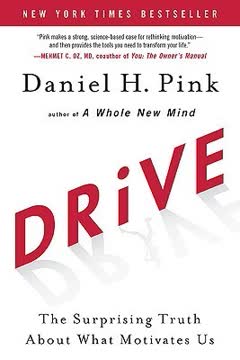
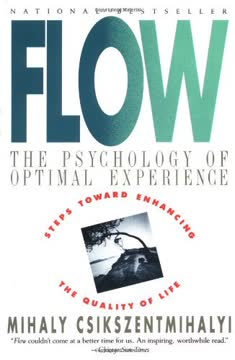
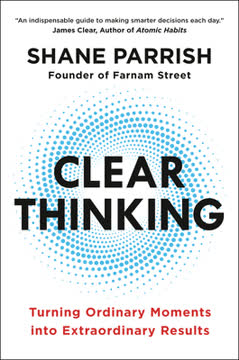
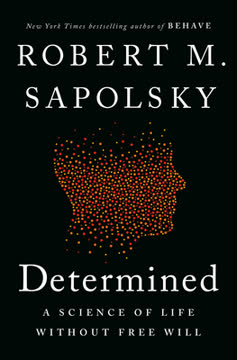
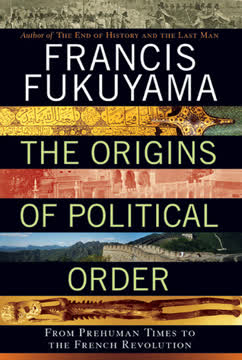
Download PDF
Download EPUB
.epub
digital book format is ideal for reading ebooks on phones, tablets, and e-readers.