Key Takeaways
1. Lean Six Sigma: Combining Efficiency and Quality for Process Excellence
Lean Six Sigma provides a rigorous and structured approach to help manage and improve quality and performance, and to solve potentially complex problems.
Synergistic methodology. Lean Six Sigma merges two powerful improvement philosophies: Lean, which focuses on eliminating waste and improving flow, and Six Sigma, which aims to reduce variation and defects. This combined approach creates a comprehensive toolkit for organizations to enhance both efficiency and quality.
Key principles. The foundation of Lean Six Sigma rests on seven principles:
- Focus on the customer
- Identify and understand how work gets done
- Manage, improve, and smooth process flow
- Remove non-value-adding steps and waste
- Manage by fact and reduce variation
- Involve and equip people in the process
- Undertake improvement activity systematically
Versatile application. Lean Six Sigma can be applied across various industries and processes, from manufacturing to services, healthcare to finance. It provides a common language and framework for improvement, enabling organizations to tackle complex problems and drive sustainable results.
2. DMAIC: A Systematic Approach to Problem-Solving and Improvement
DMAIC (Define, Measure, Analyse, Improve and Control) provides the framework to improve existing processes in a systematic way.
Structured methodology. DMAIC offers a logical and data-driven approach to problem-solving and process improvement. Each phase has specific objectives and tools:
- Define: Clarify the problem, scope, and goals
- Measure: Collect baseline data on current performance
- Analyze: Identify root causes of problems
- Improve: Develop and implement solutions
- Control: Sustain improvements and prevent regression
Iterative process. While DMAIC appears linear, it often involves iterations and revisiting earlier phases as new insights emerge. This flexibility allows teams to adapt their approach based on new information and ensures a thorough investigation of the problem.
Tollgate reviews. Regular reviews at the end of each DMAIC phase ensure project progress, alignment with objectives, and proper completion of each step. These reviews provide opportunities for course correction and stakeholder engagement throughout the improvement journey.
3. Understanding and Meeting Customer Requirements (CTQs)
CTQs help you focus on your customer requirements and provide the foundation for your measurement data.
Voice of the Customer (VOC). Capturing and translating customer needs into measurable requirements is crucial for project success. This involves various methods such as surveys, interviews, focus groups, and observations to gather customer insights.
Critical to Quality (CTQ) characteristics. CTQs are the key measurable characteristics of a product or process whose performance standards or specification limits must be met to satisfy the customer. They form the basis for measurement and improvement efforts. Developing CTQs involves:
- Identifying customer segments
- Gathering VOC data
- Translating customer needs into measurable requirements
- Prioritizing CTQs based on customer importance
Kano model. This model helps categorize customer requirements into three types:
- Must-be: Basic expectations that cause dissatisfaction if not met
- One-dimensional: Requirements that increase satisfaction linearly as performance improves
- Delighters: Unexpected features that provide high satisfaction but don't cause dissatisfaction if absent
4. Identifying Value-Added Steps and Eliminating Waste
Muda is Japanese for waste. In any process, some steps add value and some don't.
Value-added analysis. A critical step in Lean Six Sigma is distinguishing between value-added and non-value-added activities. Value-added steps must meet three criteria:
- The customer cares about the step
- The step physically changes the product/service or is an essential prerequisite
- The step is done right the first time
Seven wastes. Taiichi Ohno of Toyota identified seven common types of waste:
- Overproduction
- Waiting
- Transportation
- Processing
- Inventory
- Motion
- Correction (defects)
Waste elimination strategies. Once identified, non-value-added activities and waste can be addressed through various techniques:
- Process mapping to visualize and streamline workflows
- 5S methodology for workplace organization
- Pull systems to reduce overproduction and inventory
- Error-proofing (poka-yoke) to prevent defects
- Standardized work to reduce variation and improve efficiency
5. Utilizing Data and Statistical Tools for Informed Decision-Making
Control charts provide the only way to identify and understand variation.
Data-driven approach. Lean Six Sigma emphasizes making decisions based on facts and data rather than intuition or assumptions. This requires developing a robust measurement system and collecting relevant data throughout the improvement process.
Key statistical tools:
- Control charts: To distinguish between common cause and special cause variation
- Pareto charts: To identify the vital few causes of problems
- Histograms: To visualize data distribution
- Scatter plots: To explore relationships between variables
- Capability indices: To assess process performance relative to specifications
Understanding variation. A crucial concept in Lean Six Sigma is recognizing and properly responding to different types of variation:
- Common cause variation: Natural, expected variation inherent in the process
- Special cause variation: Unusual, assignable causes that should be investigated and addressed
By using these tools, teams can avoid the pitfalls of reacting to normal process fluctuations (tampering) while identifying true opportunities for improvement.
6. Managing Process Flow and Tackling Bottlenecks
Either you manage the bottlenecks or they manage you.
Theory of Constraints. This approach, developed by Eliyahu Goldratt, provides a framework for identifying and managing bottlenecks in processes. The five-step approach includes:
- Identify the constraint
- Exploit the constraint
- Subordinate other steps to the constraint
- Elevate the constraint
- Repeat the process
Pull systems. Implementing pull production, where each process takes what it needs from the preceding process only when needed, helps reduce work-in-progress and improve flow. This concept is often implemented using Kanban systems.
Cellular manufacturing. Organizing related activities into cells can significantly improve process flow by:
- Reducing transportation and waiting time
- Facilitating single-piece flow
- Improving communication and problem-solving
- Increasing flexibility to meet changing demand
By focusing on improving flow and addressing bottlenecks, organizations can significantly reduce lead times and improve overall process efficiency.
7. Implementing Preventive Measures and Error-Proofing
Prevention is a good way to tackle waste and delays in your processes.
Proactive approach. Lean Six Sigma emphasizes preventing problems rather than merely reacting to them. This shift in mindset can lead to significant improvements in quality and efficiency.
Key preventive techniques:
- Failure Mode and Effects Analysis (FMEA): A systematic method for identifying potential failures and their impacts
- Poka-yoke (error-proofing): Designing processes or products to prevent errors from occurring
- Jidoka: Automatically stopping processes when abnormalities occur to prevent defects from progressing
- Standardized work: Establishing and documenting best practices to reduce variation
- Preventive maintenance: Regular equipment care to prevent breakdowns and ensure reliability
Benefits of prevention. Implementing preventive measures can:
- Reduce rework and associated costs
- Improve customer satisfaction by reducing defects
- Increase process stability and predictability
- Free up resources previously devoted to firefighting
By focusing on prevention, organizations can create more robust processes that deliver consistent quality and require less intervention.
8. Engaging Leadership and Fostering a Culture of Continuous Improvement
Leadership commitment is one of these critical factors. Clinching buy-in at the beginning is the real challenge.
Leadership roles. Successful Lean Six Sigma implementation requires active involvement from leaders at all levels:
- Executive sponsors: Provide strategic direction and resources
- Deployment champions: Oversee program implementation and remove barriers
- Project champions: Support individual improvement projects
- Process owners: Ensure ongoing process management and improvement
Cultural transformation. Lean Six Sigma is not just about tools and techniques; it requires a shift in organizational culture. Key elements include:
- Empowering employees to identify and solve problems
- Encouraging data-driven decision-making
- Fostering a mindset of continuous improvement
- Recognizing and rewarding improvement efforts
- Promoting cross-functional collaboration
Sustainability. To create lasting change, organizations must integrate Lean Six Sigma principles into their daily operations and management systems. This involves aligning improvement efforts with strategic goals, developing internal expertise, and creating mechanisms for sharing best practices.
9. Selecting and Prioritizing Improvement Projects
Selecting the right areas in the business to focus on, especially when first starting up a Lean Six Sigma programme, will ensure early successes and build confidence.
Project selection process. Choosing the right projects is crucial for Lean Six Sigma success. A typical selection process involves:
- Generating a list of candidate projects
- Assessing project suitability for Lean Six Sigma
- Prioritizing projects based on strategic importance and potential impact
Selection criteria. Common factors to consider when evaluating potential projects include:
- Alignment with organizational strategy
- Potential financial impact
- Customer satisfaction improvement
- Process stability and capability
- Data availability
- Project scope and complexity
- Resource requirements
Prioritization tools. Various methods can help prioritize projects:
- Criteria selection matrix
- Benefit-effort matrix
- Pareto analysis of improvement opportunities
By carefully selecting and prioritizing projects, organizations can maximize the impact of their Lean Six Sigma efforts and build momentum for the program.
10. Addressing the Human Side of Change in Lean Six Sigma Initiatives
Almost always, if Six Sigma and Lean projects fail, people issues of one form or another are the cause.
Change management. Implementing Lean Six Sigma involves significant organizational change. Key elements of effective change management include:
- Creating a sense of urgency
- Developing a clear vision for change
- Communicating the vision effectively
- Empowering employees to act
- Generating short-term wins
- Consolidating gains and producing more change
- Anchoring new approaches in the culture
Overcoming resistance. Resistance to change is natural and should be anticipated. Strategies for addressing resistance include:
- Involving stakeholders early in the process
- Addressing concerns and fears openly
- Providing training and support
- Demonstrating the benefits of change
- Recognizing and rewarding adoption of new practices
Stakeholder analysis. Understanding and managing stakeholders is crucial for project success. This involves:
- Identifying key stakeholders
- Assessing their level of support or resistance
- Developing strategies to increase support and address concerns
- Regularly monitoring and updating stakeholder engagement plans
By effectively managing the human aspects of change, organizations can increase the likelihood of successful Lean Six Sigma implementation and create a culture of continuous improvement.
Last updated:
FAQ
What's Lean Six Sigma For Dummies about?
- Structured Improvement Approach: The book offers a structured methodology for enhancing quality and performance in organizations by combining Lean and Six Sigma principles.
- Lean and Six Sigma Focus: It integrates Lean thinking, which aims to improve process flow and eliminate waste, with Six Sigma, which focuses on reducing variation and enhancing quality.
- Practical Guidance: Provides managers and team leaders with practical tools and techniques to improve organizational efficiency and effectiveness.
Why should I read Lean Six Sigma For Dummies?
- Comprehensive Guide: Serves as a detailed resource for implementing Lean Six Sigma, breaking down complex concepts into understandable parts.
- Real-World Applications: Includes practical examples and case studies that demonstrate the application of Lean Six Sigma in various contexts.
- Improvement Framework: Introduces the DMAIC framework, essential for systematic process improvement.
What are the key takeaways of Lean Six Sigma For Dummies?
- Lean and Six Sigma Synergy: Emphasizes understanding both Lean and Six Sigma principles to enhance organizational performance.
- Customer Focus: Highlights the importance of identifying and understanding customer needs through the Voice of the Customer (VOC) and Critical To Quality (CTQ) requirements.
- Continuous Improvement Culture: Encourages a culture of continuous improvement, urging organizations to regularly assess and refine processes.
What is DMAIC in Lean Six Sigma For Dummies?
- Define, Measure, Analyze, Improve, Control: A structured problem-solving process used to improve existing processes, with each phase having specific goals and activities.
- Systematic Approach: The Define phase identifies the problem and project goals, while the Measure phase involves data collection to understand current performance.
- Root Cause Analysis: The Analyze phase identifies root causes, followed by the Improve phase for developing solutions, and the Control phase to sustain improvements.
What is DMADV in Lean Six Sigma For Dummies?
- Define Phase: Similar to DMAIC, it involves defining project goals and customer requirements, setting the foundation for designing new processes or products.
- Measure Phase: Focuses on measuring customer needs and translating them into specific, measurable characteristics to ensure the design meets expectations.
- Analyze Phase: Evaluates potential design concepts against customer requirements to identify the best options that satisfy CTQs.
How does [Book Title] define Lean thinking?
- Enhancing Customer Value: Lean thinking is about enhancing value for the customer by improving process flow and eliminating waste.
- Historical Context: Traces Lean thinking back to the Toyota Production System, which revolutionized manufacturing with a focus on efficiency and quality.
- Versatile Application: While often associated with manufacturing, Lean principles can be applied in service organizations and various sectors.
What are Critical To Quality (CTQ) requirements in [Book Title]?
- Customer-Centric Measures: CTQs are measurable requirements that express what is critical to the customer’s perception of quality.
- Foundation for Measurement: They provide the basis for developing performance measures, ensuring organizations can assess how well they meet customer expectations.
- Dynamic Nature: CTQs can evolve over time as customer needs change, highlighting the importance of regularly revisiting these requirements.
What is the Voice of the Customer (VOC) in the context of [Book Title]?
- Understanding Customer Needs: VOC involves gathering customer feedback to understand their needs, preferences, and expectations.
- Methods of Collection: Discusses various methods for collecting VOC, such as interviews and surveys, emphasizing translating feedback into actionable requirements.
- Avoiding Assumptions: Warns against assuming customer needs, advocating for direct engagement to accurately capture them.
How does [Book Title] address process mapping?
- Visualizing Processes: Highlights the importance of process mapping to visualize how work gets done, aiding in identifying inefficiencies.
- Types of Maps: Introduces different types of process maps, like deployment flowcharts and value stream maps, to illustrate process flow.
- Gemba Visits: Encourages visiting the Gemba to observe processes firsthand, ensuring maps reflect reality rather than assumptions.
What are control charts, and why are they important in [Book Title]?
- Identifying Variation: Control charts monitor process variation over time, helping distinguish between common and special cause variation.
- Statistical Control: A process in statistical control is predictable and stable, essential for effective management and improvement.
- Actionable Insights: They help identify when to take action to improve processes and ensure sustained improvements.
How can I overcome resistance to change in Lean Six Sigma?
- Build Relationships: Establish trust and open communication with employees to alleviate fears about change.
- Communicate Clearly: Provide clear information about the reasons for change and expected benefits, reducing uncertainty.
- Celebrate Successes: Recognize and celebrate small wins to motivate employees and reinforce the value of changes.
What are some common pitfalls to avoid in Lean Six Sigma projects?
- Jumping to Solutions: Avoid rushing to solutions without thorough analysis, which can lead to ineffective outcomes.
- Overcomplicating Processes: Adding unnecessary steps can create confusion; Lean Six Sigma emphasizes simplicity.
- Ignoring People Issues: Focusing solely on technical aspects without addressing human factors can lead to resistance and failure.
Review Summary
Lean Six Sigma For Dummies receives mixed reviews, with readers finding it a solid introduction to the methodology but often dry and challenging to apply. Some appreciate its approachability and valuable analytical tools, while others struggle with its relevance to modern business practices. Readers note its usefulness for beginners and as a quick review guide. However, some find the content outdated and difficult to implement in non-manufacturing environments. Overall, the book is seen as a decent starting point for those new to Lean Six Sigma concepts.
Similar Books
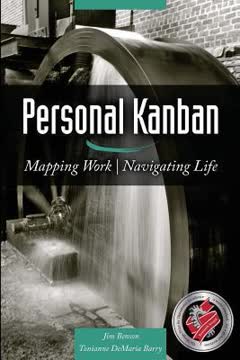
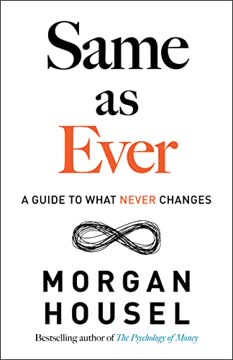
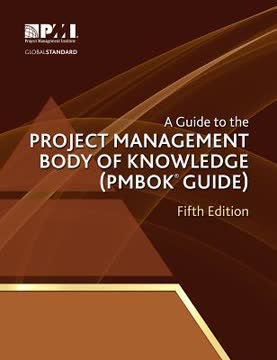
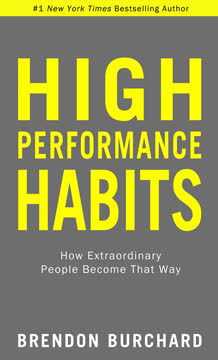
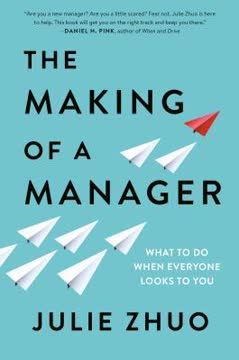
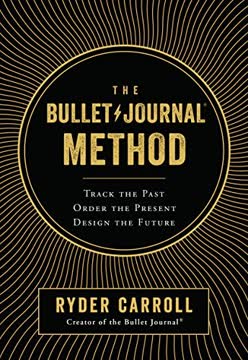
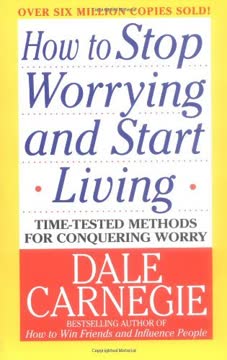
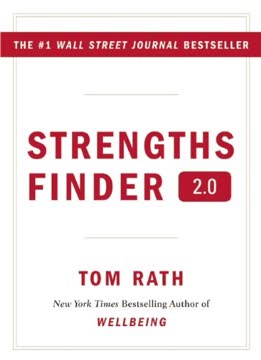
Download PDF
Download EPUB
.epub
digital book format is ideal for reading ebooks on phones, tablets, and e-readers.