Key Takeaways
1. Develop a long-term philosophy focused on creating value
Toyota always starts with the goal of generating value for the customer, society, and the economy.
Long-term thinking. Toyota's philosophy goes beyond short-term financial goals. The company sees itself as having a larger purpose to contribute value to customers, employees, and society. This long-term orientation allows Toyota to make decisions and investments that may not pay off immediately, but create sustainable success.
Value creation focus. Rather than fixating solely on profits, Toyota aims to generate value in multiple ways:
- For customers: High-quality, innovative products
- For employees: Job security, skills development
- For society: Economic growth, technological progress
- For the environment: More efficient, less polluting vehicles
This philosophical foundation shapes Toyota's approach to business decisions, guiding the company to prioritize long-term value over short-term gains.
2. Create continuous process flow to surface problems
Flow is most evident in the Toyota Production System, but it is also evident throughout Toyota in the organizational culture, which has a focus on value-added flow as an alternative to the normal stop/start approach to working on projects a little bit at a time.
Establishing flow. Toyota strives to create smooth, continuous flow in all processes - from manufacturing to product development to administrative work. This means eliminating delays, batches, and inventory between steps.
Surfacing problems. The real power of flow is that it quickly exposes any issues or inefficiencies in the process. When one part of the process stops, the entire flow is disrupted, making problems immediately visible and creating urgency to solve them. This allows Toyota to:
- Identify and address problems rapidly
- Continuously improve processes
- Develop problem-solving capabilities in employees
By creating flow, Toyota transforms its entire organization into a finely-tuned system for continuous improvement and learning.
3. Use pull systems to avoid overproduction
Toyota found a better approach, modeled after the American supermarket system. Stock relatively small amounts of each product and restock the supermarket shelf frequently, based on what the customer actually takes away.
Pull principle. Toyota uses a pull system where production is triggered by actual customer demand, rather than forecasts. This is modeled on supermarkets, which restock shelves based on what customers buy.
Key aspects of Toyota's pull system:
- Kanban cards signal when to produce/move materials
- Small amounts of inventory at each stage
- Frequent replenishment in small batches
- Production paced to actual customer demand (takt time)
Benefits of the pull approach:
- Reduces overproduction and excess inventory
- Improves cash flow by reducing working capital tied up in inventory
- Increases flexibility to respond to changes in demand
- Surfaces problems that were previously hidden by excess inventory
By producing only what is needed when it is needed, Toyota avoids the waste of overproduction while staying responsive to customer needs.
4. Level out the workload (heijunka)
Smoothing demand for upstream processes
Smoothing production. Heijunka refers to leveling out the production schedule in terms of both volume and product mix. Even if customer demand fluctuates, Toyota tries to keep a steady, level schedule.
Key aspects of heijunka:
- Produce in small batches to maintain mix
- Use a heijunka box to visually manage the production sequence
- Buffer fluctuations with strategic inventory
Benefits of leveling:
- Reduces burden on people and equipment
- Enables standardized work
- Smooths demand on suppliers
- Minimizes inventory while maintaining flexibility
While it may seem counterintuitive to not produce exactly to customer demand, leveling creates stability that enables Toyota to be more efficient and responsive overall.
5. Build a culture of stopping to fix problems
Toyota sees it as an opportunity to identify a weakness within the system, to attack the weakness, and to strengthen the overall system.
Stop and fix. Toyota empowers workers to stop production when they spot a problem, rather than letting defects continue down the line. This may seem costly in the short-term, but pays off through higher quality and continuous improvement.
Key elements of Toyota's problem-solving culture:
- Andon cords allow any worker to stop the line
- Leaders quickly respond to andon calls
- Root cause analysis to prevent recurrence
- Errors seen as system failures, not individual faults
- Celebration of problem identification
This approach turns every employee into a quality inspector and problem solver, dramatically improving quality while developing people's capabilities.
6. Standardize tasks for continuous improvement
Standardization is actually the starting point for continuous improvement.
Standardized work. Toyota views standardization not as a rigid constraint, but as the foundation for kaizen (continuous improvement). By defining the current best practice, it becomes possible to improve upon it.
Key aspects of Toyota's approach to standardization:
- Detailed definition of work steps, timing, and outcomes
- Worker involvement in creating and updating standards
- Visual management to make standards clear
- Frequent auditing to ensure adherence
- Standards seen as temporary, always subject to improvement
Benefits of this approach:
- Ensures consistency and quality
- Makes abnormalities immediately obvious
- Provides a stable base for experimentation and improvement
- Allows best practices to be easily shared
By standardizing work, Toyota creates a dynamic tension between current standards and ideas for improvement, driving continuous progress.
7. Use visual control so no problems are hidden
People looking at well-designed charts on a wall can have very effective discussions.
Visual management. Toyota makes extensive use of visual controls to make the status of processes immediately apparent to everyone. This supports the principle of surfacing problems quickly.
Examples of visual controls at Toyota:
- Andon boards showing line status
- Kanban cards signaling production needs
- Heijunka boxes displaying production schedules
- 5S color-coding and markings
- Performance boards tracking key metrics
- A3 reports summarizing projects visually
Benefits of visual control:
- Problems become immediately obvious
- Enhances communication and alignment
- Supports fact-based decision making
- Empowers workers to manage their own areas
By making information visual and accessible, Toyota creates an environment where problems can't hide and everyone can contribute to improvement.
8. Use only reliable, thoroughly tested technology
Toyota has had experience with pushing the latest and greatest technology, and now avoids repeating this mistake.
Thoughtful adoption. While Toyota is a leader in many technologies, it is cautious about adopting new tech in its core processes. New technology is thoroughly vetted to ensure it truly serves the needs of the people and processes.
Toyota's approach to technology:
- Proven reliability is prioritized over novelty
- New tech must clearly support Toyota Way principles
- Extensive testing before full implementation
- Preference for flexible, right-sized equipment
- Focus on how tech supports/develops human capabilities
This approach helps Toyota avoid:
- Disruptions from immature technology
- Dependence on inflexible, complex systems
- Technology that inhibits continuous improvement
By carefully evaluating technology through the lens of its principles, Toyota ensures that new tools enhance rather than detract from its core strengths.
9. Grow leaders who thoroughly understand the work and live the philosophy
Leaders at Toyota are grown; they are not bought.
Developing leaders. Toyota invests heavily in growing leaders from within who deeply understand the work and embody the Toyota Way philosophy. This ensures continuity of culture and approach.
Key aspects of Toyota's leadership development:
- Leaders expected to have deep technical knowledge
- Extensive job rotation to build broad understanding
- Expectation to teach and develop others
- Long apprenticeship periods (e.g. 10 years) before senior roles
- Leaders judged on their ability to develop people
Benefits of this approach:
- Leaders can effectively coach and problem-solve
- Consistent application of Toyota Way principles
- Strong alignment between all levels of the organization
- Sustainability of the culture and methods long-term
By growing leaders who live and breathe its philosophy, Toyota creates alignment and continuity that sustains its approach across generations.
10. Develop exceptional people and teams
Toyota stresses the inclusion of self-inspection in all standardized work.
People development. Toyota views its people as its most crucial asset and invests heavily in their development. This goes beyond just technical skills to developing problem-solving capabilities and teamwork.
Key elements of Toyota's approach:
- Extensive initial training (e.g. several months for new hires)
- Continuous skill development through job rotation
- Problem-solving expected at all levels
- Quality circles for team-based improvement
- Suggestion systems to leverage every employee's ideas
Benefits:
- Highly skilled, flexible workforce
- Strong problem-solving capabilities throughout the organization
- High levels of employee engagement and retention
- Continuous flow of improvement ideas
By developing exceptional people and teams, Toyota creates a powerful engine for continuous improvement and adaptation.
11. Respect your extended network of partners and suppliers
A partner becomes an extension of Toyota.
Supply chain development. Toyota views its suppliers as long-term partners to be developed, not just sources of low-cost parts. This approach extends the Toyota Production System beyond the company's walls.
Key aspects of Toyota's supplier relationships:
- Long-term partnerships vs. frequent rebidding
- Extensive sharing of Toyota Production System knowledge
- Joint problem-solving and improvement activities
- Expectation of continuous cost reduction through kaizen
- Suppliers included in early stages of product development
Benefits:
- Higher quality and reliability from suppliers
- Faster innovation and problem-solving
- More stable supply chain
- Shared continuous improvement culture
By respecting and developing its extended network, Toyota creates a larger ecosystem that operates on Toyota Way principles.
12. Go and see for yourself to thoroughly understand the situation (genchi genbutsu)
There is a basic belief in Toyota that people solving problems and making decisions need to have a deep understanding that can only come from personally verified data: seeing for yourself.
Direct observation. Toyota emphasizes the importance of going to the actual place where work is done to observe and understand first-hand. This applies to everyone from shop floor workers to top executives.
Key aspects of genchi genbutsu:
- Managers expected to regularly visit the gemba (actual place)
- Decisions based on first-hand observation, not just reports
- Problems studied where they occur, not in conference rooms
- "5 Whys" analysis conducted at the source of issues
- Respect for the knowledge of front-line workers
Benefits:
- More accurate understanding of situations
- Better decision-making
- Faster problem-solving
- Stronger connection between management and front lines
By insisting on first-hand observation, Toyota ensures that its improvement efforts and decisions are grounded in reality rather than assumption.
Last updated:
FAQ
What's The Toyota Way Fieldbook about?
- Practical Guide: The Toyota Way Fieldbook by Jeffrey K. Liker is a practical guide for implementing Toyota's management principles, focusing on the 4Ps: Philosophy, Process, People/Partners, and Problem Solving.
- Lean Manufacturing: It emphasizes learning from Toyota's success in lean manufacturing and how these principles can be applied to various organizations.
- Cultural Insights: The book delves into the cultural aspects of Toyota, highlighting the importance of leadership, employee involvement, and a shared vision for success.
Why should I read The Toyota Way Fieldbook?
- Proven Success Model: The book provides insights into a proven model of success that has transformed Toyota into a global powerhouse in manufacturing.
- Applicable Across Industries: The principles outlined can be applied beyond automotive manufacturing, making it relevant for any organization looking to improve efficiency and quality.
- Actionable Strategies: It offers practical tools and strategies that can be implemented in your organization to enhance efficiency and quality.
What are the key takeaways of The Toyota Way Fieldbook?
- Continuous Improvement: A core takeaway is the concept of continuous improvement (kaizen), which encourages organizations to constantly seek ways to enhance processes and eliminate waste.
- Employee Empowerment: The book emphasizes the importance of empowering employees at all levels to identify problems and contribute to solutions, fostering a culture of collaboration.
- Long-Term Philosophy: It stresses the importance of having a long-term corporate philosophy that prioritizes value creation for customers and society over short-term profits.
What is the 4P model in The Toyota Way Fieldbook?
- Philosophy: Focuses on the company's purpose and values, guiding all decisions and actions.
- Process: Emphasizes the importance of following the right processes to achieve desired results, highlighting the need for continuous flow and waste reduction.
- People/Partners: Stresses the development of people and partnerships, recognizing that growth and improvement come from challenging and empowering employees and suppliers.
- Problem Solving: Continuous problem-solving is essential for organizational learning, ensuring that root causes are addressed to prevent recurrence.
How does The Toyota Way Fieldbook define waste?
- Seven Types of Waste: Identifies seven types of waste: overproduction, waiting, transportation, overprocessing, excess inventory, unnecessary movement, and defects.
- Eighth Waste: Introduces an eighth waste: unused employee creativity, emphasizing the importance of engaging employees in problem-solving.
- Focus on Overproduction: Overproduction is considered the worst waste as it leads to other forms of waste, such as excess inventory and waiting times.
What is the significance of standardized work in The Toyota Way Fieldbook?
- Foundation for Improvement: Standardized work is described as the foundation for continuous improvement, allowing for consistent performance and the identification of waste.
- Visual Control: Emphasizes the need for visual controls to ensure adherence to standards, making deviations easily recognizable.
- Empowerment and Engagement: Standardized work empowers employees by providing clear expectations and a basis for improvement.
What is the Plan-Do-Check-Act (PDCA) cycle in The Toyota Way Fieldbook?
- Structured Approach: The PDCA cycle is a structured approach to problem-solving and continuous improvement, consisting of four stages: Plan, Do, Check, and Act.
- Implementation Focus: In the planning phase, teams develop an action plan based on identified problems. The "Do" phase involves implementing the plan, while "Check" assesses the results against expectations.
- Iterative Process: The "Act" phase involves making necessary adjustments based on the results, creating an iterative process that fosters ongoing improvement.
What is the concept of "genchi genbutsu" in The Toyota Way Fieldbook?
- Go and See: "Genchi genbutsu" translates to "go and see," emphasizing the importance of firsthand observation in understanding processes and identifying problems.
- Data-Driven Decisions: Encourages leaders and team members to gather data and insights directly from the work environment rather than relying solely on reports or secondhand information.
- Continuous Learning: Fosters a culture of continuous learning and improvement, as individuals are encouraged to engage with the actual work being done.
How does The Toyota Way Fieldbook address supplier partnerships?
- Long-Term Relationships: Highlights Toyota's commitment to developing long-term partnerships with suppliers rather than focusing solely on cost.
- Supplier Development: Toyota invests in the capabilities of its suppliers through training and joint improvement activities, aligning their processes with Toyota’s standards.
- Shared Goals: Emphasizes shared goals for cost reduction and quality improvement, with Toyota working closely with suppliers to set realistic targets.
How can organizations implement the principles from The Toyota Way Fieldbook?
- Start with Leadership: Develop strong leadership that embodies the principles of TPS, committed to continuous improvement and actively supporting their teams.
- Focus on Training: Implement structured training programs like Job Instruction Training to ensure that employees understand their roles and responsibilities.
- Encourage Participation: Foster a culture where all employees are encouraged to participate in improvement activities, empowering them to contribute ideas and solutions.
What are some common traps to avoid when implementing lean practices from The Toyota Way Fieldbook?
- Overemphasis on Tools: Avoid focusing too much on lean tools without understanding the underlying principles and philosophy.
- Ignoring Stability: Attempting to implement flow before achieving process stability can lead to chaos and failure.
- Misunderstanding Standardization: Misconceptions about standardization can lead to resistance; it should be viewed as a tool for improvement rather than a means of control.
What are the best quotes from The Toyota Way Fieldbook and what do they mean?
- “The Toyota Way is about tacit knowledge, not explicit procedural knowledge.”: Emphasizes that true understanding comes from experience and practice rather than just following written procedures.
- “Please try and do your best.”: Reflects Toyota's culture of continuous improvement, encouraging employees to experiment and learn from their experiences.
- “Every problem is an improvement opportunity.”: Highlights the belief that challenges should be viewed as chances to learn and enhance processes, fostering a proactive approach to problem-solving.
Review Summary
The Toyota Way Fieldbook receives high praise from readers, with an average rating of 4.18/5. Many find it an essential read for those implementing lean principles in manufacturing. Reviewers appreciate its practical approach, detailed examples, and tactical guidance for applying Toyota's methods. Some note it's best suited for those already familiar with lean concepts. A few criticize its length and repetitiveness. Overall, readers value the book's insights on continuous improvement, waste reduction, and building an effective organizational culture.
Similar Books
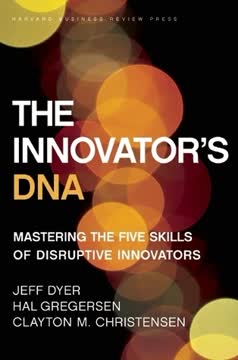
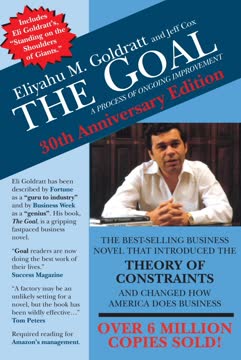
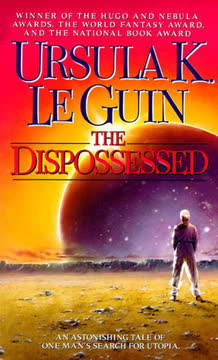
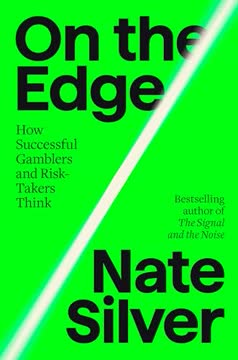
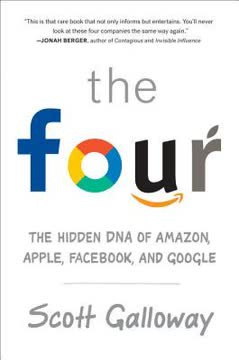
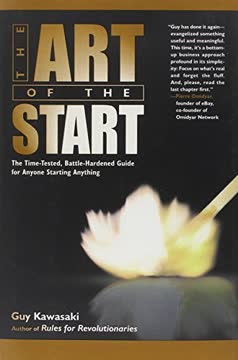
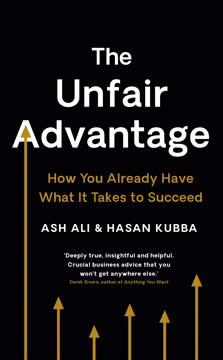
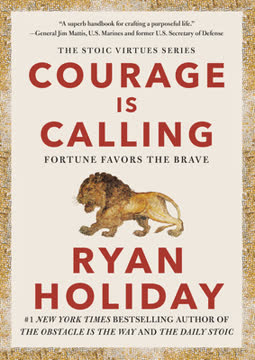
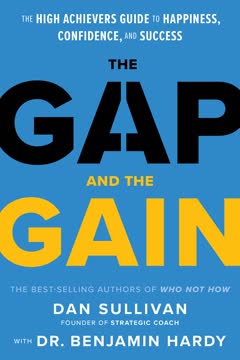
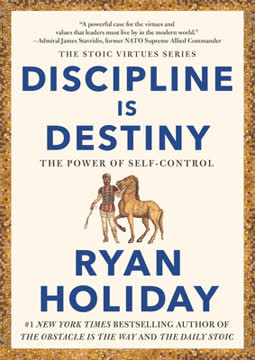
Download PDF
Download EPUB
.epub
digital book format is ideal for reading ebooks on phones, tablets, and e-readers.