Key Takeaways
1. Shift from Long Weekly Meetings to Short Daily Huddles
For the last several years now, instead of having one long subcontractor meeting each week, like the one you had yesterday, I have a fifteen-minute meeting with the trades every morning.
Frequent, focused meetings. Replace lengthy, often unproductive weekly subcontractor meetings with brief, daily huddles. These 15-20 minute stand-up meetings, ideally held at the start of the day, ensure consistent, timely communication and coordination among all trades on site.
Structured agenda is key. To keep the huddle short and effective, follow a consistent format. Each trade leader quickly shares:
- What they are working on
- Where they are working
- How many crew members are on site
- What constraints or needs they have
- Upcoming material deliveries
Encourage engagement. Remove chairs to keep everyone standing and focused. Use tools like an egg timer to enforce the time limit and the "ELMO" (Enough, Let's Move On) rule to table discussions not relevant to the whole team, moving them to a "parking lot" for later resolution.
2. Make Communication Visual for Clarity and Collaboration
At your next huddle, ask each trade foreman to come up to the board and indicate what his activity is, where he is working, how many people he’ll have for the activity, and what is in his way.
Visual tools enhance understanding. Supplement verbal communication with visual aids in the job trailer. Using laminated floor plans or elevations allows trades to mark up their planned work areas, crew sizes, and constraints directly on the drawings using color-coded dry erase markers.
Bridge communication gaps. Visual communication helps overcome language barriers and ensures everyone clearly sees where different trades will be working. This reduces misunderstandings, prevents conflicts, and facilitates better coordination between teams working in adjacent or sequential areas.
Increase accountability. When trades visually commit to their work areas and constraints on a shared board, it creates a public commitment to the team. This transparency encourages follow-through and allows others to anticipate potential conflicts proactively.
3. Identify and Eliminate the Eight Deadly Wastes (DOWNTIME)
Waste is anything that doesn’t add value—or, to put it this way, waste only ADDS time and cost to your project.
Recognize non-value activities. Learn to identify the "Eight Deadly Wastes" prevalent in construction, remembered by the acronym D.O.W.N.T.I.M.E. Eliminating these wastes is crucial for improving efficiency, reducing costs, and staying on schedule.
DOWNTIME breakdown:
- Defects: Rework or scrapped materials due to errors.
- Overproduction: Building or procuring items too early or in excess.
- Waiting: Idle time due to delays or lack of resources.
- Non-Utilized Talent: Not leveraging workers' full skills or input.
- Transportation: Unnecessary movement of materials.
- Inventory: Excess materials on site causing clutter or damage risk.
- Motion: Unnecessary movement by workers.
- Excess Processing: Doing more work than required (e.g., rework).
Impact on projects. These wastes directly add time and cost without adding value. Identifying them, like seeing excess ductwork causing delays and damage, allows teams to address root causes and improve workflow reliability.
4. Proactively Manage and Track Constraints Visually
This constraint process will be tough for some team members to get used to, as many are not used to this level of transparency or accountability.
Centralize issue tracking. Use a dedicated constraint board, visible to the entire team, to capture and track issues hindering progress. This board typically includes columns for:
- What the constraint is
- Where it is located
- Who is responsible for resolving it
- When it is expected to be resolved
Drive accountability. Assigning ownership ("Who") and setting a deadline ("When") for each constraint creates clear accountability. Reviewing the board daily ensures issues stay visible and progress is tracked, preventing them from falling through the cracks.
Empower the team. Encourage trades to add their own constraints to the board. This empowers them to voice issues and fosters a culture where the team collectively works to remove roadblocks, rather than relying solely on the superintendent.
5. Embrace Pull Planning for Team Ownership of the Schedule
On my projects, the trades and the client have the exact same schedule. There are no secrets between us. In fact, we make the schedule together.
Shift from push to pull. Move away from a "push" schedule, where dates are dictated from the top down based on forecasts. Adopt a "pull" approach, where the schedule is built backward from milestones, driven by the needs and commitments of the teams doing the work.
Collaborative scheduling. Conduct pull planning sessions with trade partners (the "last planners") to collectively build the schedule. Using sticky notes representing activities, durations, and hand-offs, the team sequences the work backward from a key milestone.
Gain buy-in and reliability. When the people performing the work define the activities, durations, and dependencies, they gain ownership and are more likely to commit to the schedule. This process reveals workflow issues and constraints that top-down planning often misses, leading to a more realistic and reliable plan.
6. Implement the Holistic Last Planner System™ Framework
The Last Planner System is holistic, and all facets of it must be utilized to leverage its maximum potential.
Integrated planning system. The Last Planner System™ (LPS) is a comprehensive production control system for construction, moving beyond just the initial master schedule. It involves a continuous cycle of planning, commitment, and learning.
Five core components:
- Master Scheduling: High-level project milestones and overall duration.
- Phase Scheduling (Pull Planning): Detailed collaborative planning for specific project phases or milestones.
- Look Ahead Planning: Developing a 6-week rolling window of upcoming work, identifying constraints.
- Weekly Work Planning: Detailed commitments by last planners for the upcoming week, identifying make-ready needs.
- Percent Plan Complete (PPC): Measuring the reliability of weekly commitments and analyzing reasons for failure.
Continuous flow. Each component feeds into the next, creating a feedback loop. The master schedule informs phase planning, which informs the look-ahead, which informs weekly plans, and PPC measures the success of the weekly plans, providing data for continuous improvement.
7. Measure Planning Reliability with Percent Plan Complete (PPC)
Percent Plan Complete measures how well the planning on a job is working.
Track commitment reliability. Percent Plan Complete (PPC) is a metric used to measure the percentage of planned activities that were actually completed in a given week. It is calculated by dividing the number of completed activities by the total number of planned activities.
Focus on planning, not just production. PPC is not a production tracker or a report card for individual trades. Its primary purpose is to assess the reliability of the planning process. A low PPC indicates issues in planning, constraint removal, or making reliable commitments.
Analyze root causes. The real value of PPC comes from analyzing why commitments were missed. Common root causes include:
- Weather
- Manpower issues
- Machinery problems
- Design conflicts
- Make-ready needs (dependencies)
- Material delays
- Poor scheduling/commitment
Understanding these root causes allows the team to address systemic issues and improve future planning and execution reliability.
8. Foster a Culture of Respect and Empower Trade Partners
What I have learned is that we are so much better with everyone participating—everyone in the field having a voice, empowered to make decisions, and being accountable.
Value all contributions. Recognize that trade partners (the "last planners") are the experts in their craft and hold the most valuable knowledge about how the work gets done in the field. Treat them as partners, not just subcontractors following orders.
Empower decision-making. Give trade foremen a voice in planning and problem-solving processes, such as daily huddles, constraint management, and pull planning. Empowering them to make commitments and resolve issues directly improves morale and project outcomes.
Build trust and teamwork. Open communication, transparency (like sharing the real schedule), and mutual respect build trust within the team. When challenges arise, a strong team culture encourages members to support each other, even stepping outside their typical roles to ensure project success.
9. Commit to Continuous Improvement and Sharpen Your Axe
He taught me that one of us worked harder and the other worked smarter, and that smart working beats hard working any day of the week.
Work smarter, not just harder. The story of sharpening the axe illustrates the principle of continuous improvement. Regularly investing time and effort into improving processes, tools, and skills (sharpening the axe) is more effective in the long run than simply working harder with outdated or inefficient methods.
Embrace learning from failures. View setbacks and missed commitments (identified through PPC analysis) as opportunities to learn and improve. Analyze root causes without blame and adjust planning processes, communication methods, or resource allocation accordingly.
Journey, not a destination. Implementing Lean principles and the Last Planner System is an ongoing journey. It requires perseverance, a willingness to experiment, and a commitment to constantly seek better ways of working. The payoff is not just improved project performance but also reduced stress and increased job satisfaction.
Last updated:
Review Summary
The Lean Builder receives positive reviews for its accessible introduction to Lean construction principles. Readers appreciate the fable format, making complex concepts easily digestible. Many find it valuable for construction professionals, especially superintendents and project managers. The book's focus on visual tools, daily huddles, and "Pull Planning" is highlighted. While some reviewers note its narrow focus and potential over-optimism, most recommend it for those in the construction industry looking to implement Lean practices. The audiobook narration also receives praise for its performance.
Similar Books
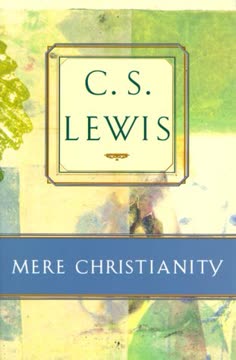
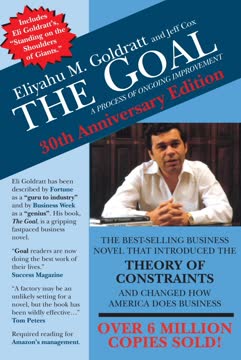
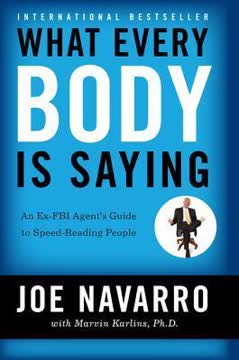
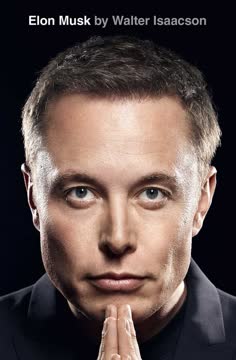
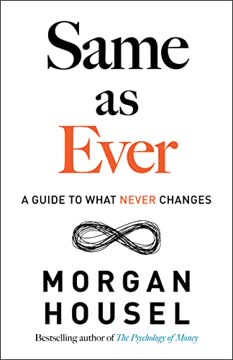
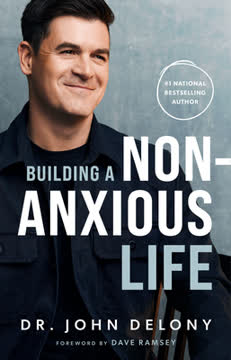
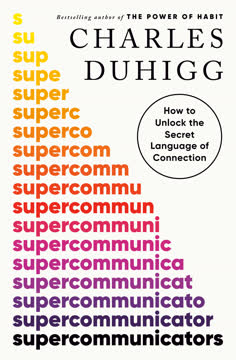
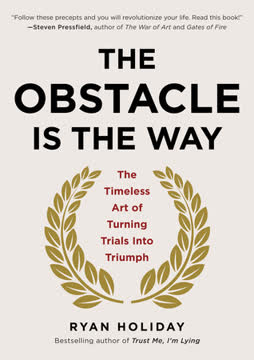
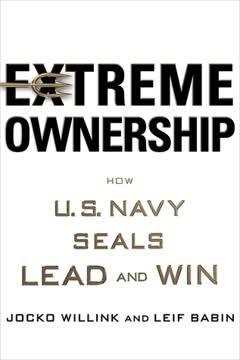
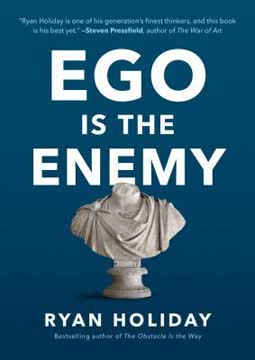
Download PDF
Download EPUB
.epub
digital book format is ideal for reading ebooks on phones, tablets, and e-readers.